Choosing the best metal to cast is based on the parts size, complexity and volume. These factors all affect the necessary temperatures, molding and casting processes it will take to achieve your final product. Certain more malleable metals will be easier to work with in an at home workshop and others may require more tools and additional work that is only appropriate for a professional or commercial workshop and therefore it is vitally important to do as much research as possible into which metal you choose for your project.
Some examples of this is that you may need a metal that is more malleable and easily liquefied for more intricately detailed products such as jewellery, whereas this may not be as necessary for sculpture making or furniture building but these materials would need to have more durability and sturdiness once cast.
In addition to choosing your metal, you may need to choose additives to achieve your desired final effect. This is not completely necessary and will only depend on the final look you are going for. These can include chemicals and colourants that are particularly important for sculptures and artistic projects. It is important to use an extremely disciplined process of production and control in order to ensure utmost safety and satisfaction throughout your metal casting.
Why choose Bronze Casting?

Source: commsp
Copper alloys are amongst the easiest metals to cast and bronze is included in this making it an extremely popular choice for both homemade casting and professional needs. Having been practiced for centuries bronze castings have frequently been used throughout history for sculpture making and furniture. It requires a lower temperature to reach its melting point in comparison to other popular metals making it more energy efficient and easier to use. Certain compositions of bronze do not change when melted making it an ideal metal for casting. However, bronze alloys can expand a very small amount before they cool which allows it to fill in smaller details in a mould. The shrinking allows it to be separated from its casting mold. Despite the fact it is easily malleable and lends itself to the molding and casting process due to its ability to be liquefied at a lower temperature, is also very strong in comparison to other materials that have been used for sculpture making etc. making it an excellent choice for these reasons. The bronze can be highly polished making it a good choice for artistic purposes. Bronze is also relatively resistant to corrosion giving it excellent longevity.
If you are lacking in experience bronze casting is a great starting point to practice. It is less dangerous than other ways of casting and uses materials that are more reasonable (particularly the choice of metals) so allows for some mistakes in the early stages. Because the bronze composition isn’t altered when repeatedly melting it, you can therefore reuse some of your metal if you were to make a mistake during your project without wasting any materials making this extremely efficient in comparison to using metals that are more difficult to work with in the long run.
Copper, brass, aluminium, pewter and silver are some other metals that you may want to trial as they are argued to be easy to cast. However, some of these have higher melting points making them more dangerous to work with and therefore are only recommended for professionals. In addition to this, some metals require different tools and appliances as well as a variation in casting processes so it is advisable to have some experience before trying to branch out into some of these, especially if you’re planning on doing it at home. Metals like silver are also known to be more temperamental to work with so you may find some mistakes or discrepancies in your final products and as it cannot be re-melted as often as bronze or other copper alloys you may find yourself wasting materials and having a less efficient workspace.
Casting Processes
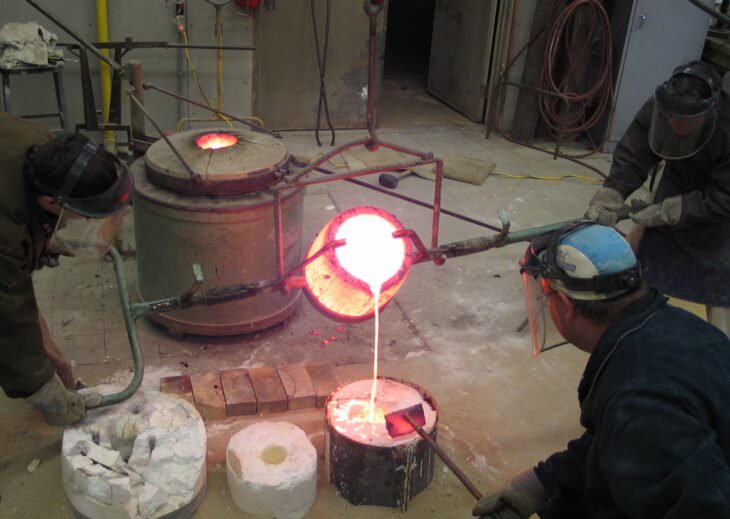
Source: emich
Sand casting is one of the most commonly used casting processes. It requires heating up the metal alloy using a furnace and dispersing it into a chamber inside a sand mold. The mold can then be separated in half to remove the solid metal cast inside. This process can be used for almost any size casting from extremely tiny to almost 1000kg’s. The cast metal can then be machined as necessary and pressure tested to ensure its durability for shipping and its intended use.
Alternative methods to sand casting include using wax/plaster or a centrifuge. The choice between these methods usually depends on the level of detail needed to be cast. A centrifuge casting can generally provide a higher level of detail as the hotter more controlled temperature allows for the metal to melt into the finer carved details. Visit here for more details.
Wax casting is often used with bronze casting as it allows for getting all of the molten bronze into the small details of your cast through the use of wax tubes. Wax can also be smoothed out to achieve a perfected outer shell. One drawback of this is that the molds usually don’t hold up and cannot be used again, so may not be the ideal choice if you are looking for consistency and continuity in your products.
Choosing The Easiest Metal To Cast
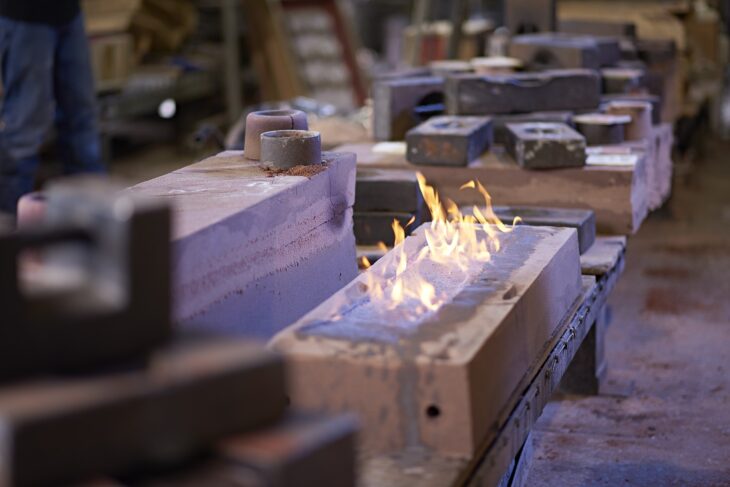
Source: novacast
Be sure to do plenty of research on which metal is best for your project and the ideal casting process to choose and if you’re unsure always consult with a professional. Bronze casting is an excellent choice for most experience levels and both home workshops and commercial professionals for a variety of types of project and when used in a sand casting process can achieve excellent results as long as proper safety precautions are followed throughout. If you want to experiment why not try a variety of bronze casting to gain some experience and see what you can achieve!