Humanity has been using machines for centuries, to process wood, metal, plastic, and other materials. However, modern equipment differs from the machines that were installed in factories in the last century. One of the key differences is automation and software control of processes.
There are many CNC machines, including lathes, milling, and other units, which are actively used in the automotive, metallurgical, heavy and light industries, in the production of aircraft parts, implants, watches, and even jewelry. Moreover, CNC machines are becoming more affordable, so much equipment is being installed more and more often in private workshops and even garages.
Why are CNC machines in such high demand nowadays? Why will automated equipment replace outdated manual electromechanical equipment in the foreseeable future?
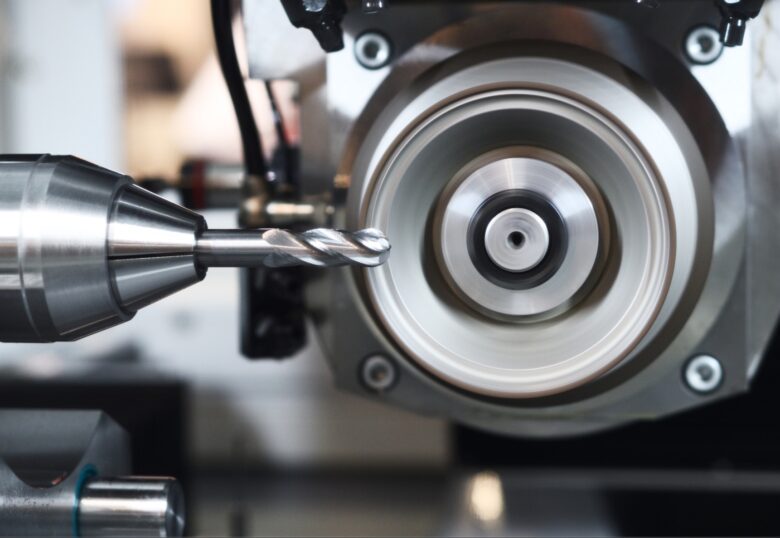
Source: canva.com
Contents [show]
Improved performance
Unlike manually controlled machines, CNC equipment can operate without breaks or days off. One qualified operator can simultaneously monitor the production process on 2 or more machines.
CNC machines can carry out several turning and milling operations at once, automatically changing tools. It speeds up the workflow.
Also, CNC milling machines process workpieces faster than a specialist, since processing does not require preliminary marking and other preparatory manipulations. At the same time, the machine can reproduce the same parts hundreds and thousands of times, exactly following the programmed algorithm.
Milling machines are used all over the world, including EU countries. For example, in France, they are called fraiseuse CNC, although the main equipment manufacturers are in Germany, Japan, the USA, and China.
High processing precision
The machine is controlled by a program containing algorithms. In this way, the CNC machine can repeat processes many times with minimal chance of error or manufacturing defects. Thanks to high-precision processing, waste is reduced, although the waste made by CNC machines is higher than with casting or 3D printing.
Automated machines produce parts of any shape, including highly complex parts. In this case, the machine will work faster and more accurately than a person.
Thanks to high precision work, the wear of the cutter and other tools is reduced. On electromechanical machines with manual control, cutters need to be changed more often, as they wear out faster. On manually operated machines, cutters and other tools wear out faster, since even experienced specialists cannot always calculate the optimal operating mode for a cutter.
Please note that processing accuracy is an important criterion for choosing a machine. Manufacturers offer machines with several accuracy classes – from standard machines to machines with increased accuracy and particularly high precision in processing parts.
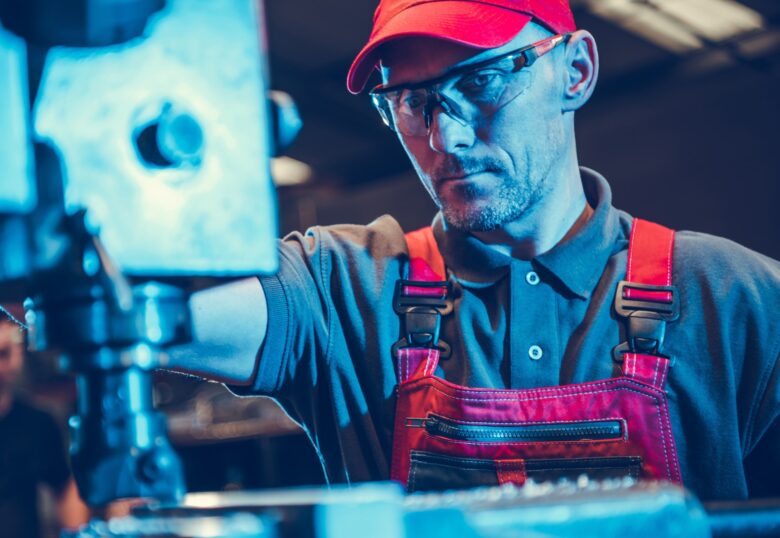
Source: canva.com
High profitability
In a highly competitive market, production should operate with maximum efficiency and profitability. Installing CNC machines to replace outdated equipment allows you to increase profitability and production volume in the long term.
By integrating modern technologies into the production process, the company can reduce the number of personnel. At the same time, labor safety increases, since the operator is not directly involved in the production process.
Another advantage of CNC machines is production flexibility. The operator can quickly change tasks for the machine, which stores in its “electronic brain” various algorithms for producing a particular part. Some machines can change tools themselves, reducing human intervention to a minimum. However, even in this case, the operator must monitor the production process to minimize the likelihood of errors and malfunctions.
The main features of CNC machines
- CNC milling and other machines are equipped with their own operating system (OS). The operator loads the program using a special system of codes that the equipment reads.
- There are several types of milling machines that differ in the location of the spindle and other design features – vertical, horizontal, with 4 and 5 axes, as well as universal.
- To control CNC milling machines, the operator must have the appropriate qualifications, as well as the skill of writing programs using a special G-codes system. At the initial stage, a virtual drawing of the part is created, which is then transferred to the machine memory using special codes and commands.
- CNC machines can process a variety of materials, including metal, wood, polymers, acrylic, and plastic.
- Depending on the model and brand, CNC milling machines may have additional functionality – an automatic tool change system, a vacuum workpiece fastening system, and so on.
Do automated control machines have any disadvantages? CNC machines are more expensive than universal manual machines. In addition, only a qualified operator can operate a CNC machine. This requires investment, both in the purchase of new equipment and in personnel training. For small industries and small businesses, this may not be profitable.
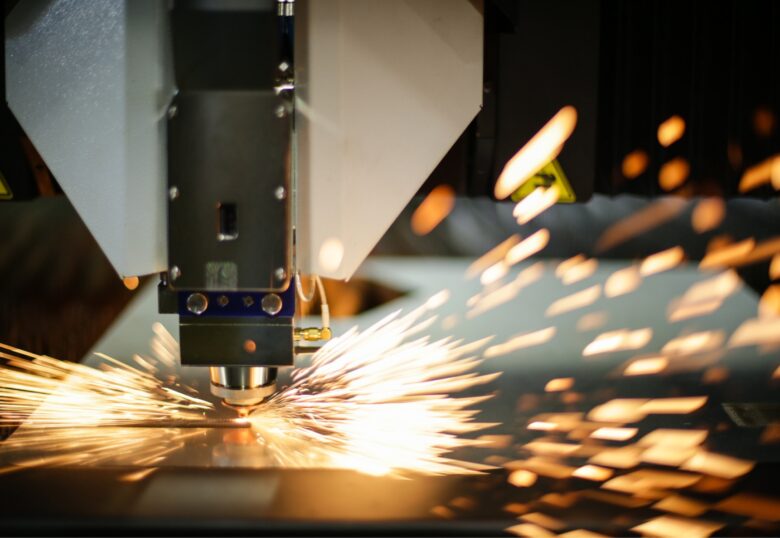
Source: canva.com
Some tips for choosing CNC milling machines
- Milling machines vary in size – from small equipment for small-scale production or home use to multi-ton stations that are used in industrial facilities for mass production.
- The set of options and functions of the machine directly depends on the model. For example, machines with three axes and a fixed spindle are suitable for simple operations, while machines with 4 and 5 axes, a remote spindle, and a rotating gantry are suitable for complex operations.
- Pay attention to the version of the software the machine is running. Manufacturers typically release software updates.
- Another important criterion is the control panel of the machines, which can be made either in the form of a touch screen or analog buttons.
- CNC machines require a stable power supply. Voltage surges can lead to equipment breakdowns. Therefore, stabilizers and uninterruptible power supplies must be installed in the electrical network of enterprises.
How to choose a CNC machine
We recommend that you contact consultants from specialized suppliers since choosing a CNC machine is impossible without skills and knowledge. It is necessary to take into account the characteristics of the production process, production volume, operator qualifications, profitability, and so on.
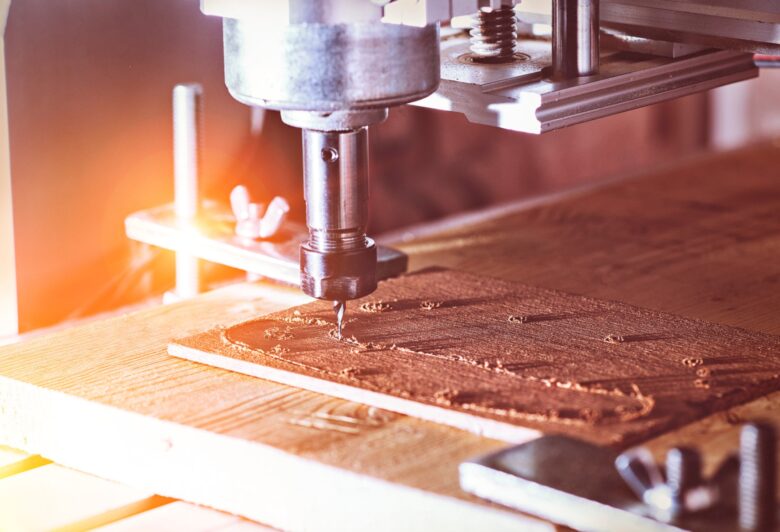
Source: canva.com
At the same time, CNC-controlled machines can significantly increase the volume of output, improve the quality of products, and make the production process almost continuous and more comfortable for personnel.