Among the many heavy-duty machines that orchestrate the symphony of construction and mining industries, stone crushers hold a place of distinction. They are the unsung heroes, tirelessly reducing large rocks into smaller fragments, ready for further processing or direct use. This piece offers an in-depth exploration of eight different types of stone crushers, shedding light on their unique features, operating principles, and applications. Buckle up for this fascinating journey into the world of stone-crushing machinery.
Contents [show]
1. Jaw Crushers
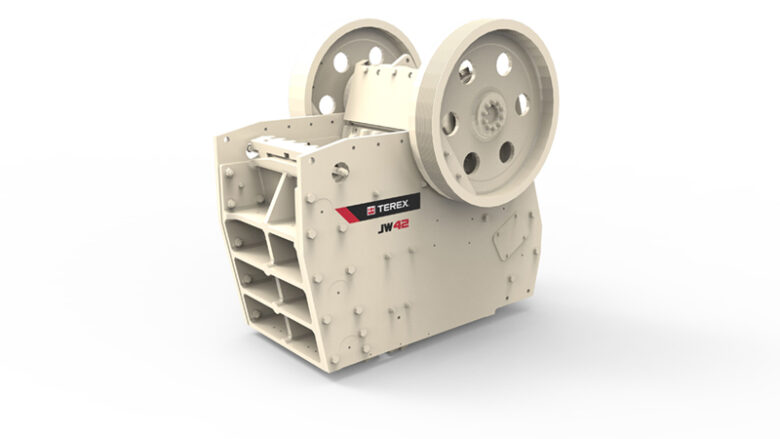
Source: terex.com
Initiating our exploration, the first stone crusher we encounter is the jaw crusher. This type of machine boasts a simplistic yet highly effective design, employing two jaws – one stationary and the other mobile – to accomplish the task of crushing. As the mobile jaw exerts force, the material lodged between the two jaws gets compressed and broken down, ideal for the first stage of size reduction in mining and construction applications.
Beyond the basics, jaw crushers are noted for their ability to crush hard, abrasive materials due to their robustness and durability. This resilience stems from the fact that the crushing occurs in a V-shaped chamber created by the two jaws. The larger rocks are broken down at the top of the ‘V’, with the fragments then moving downwards where they are further crushed into smaller pieces. The design, functionality, and robustness of the jaw crusher make it an essential component in many crushing operations.
2. Impact Crushers
Our exploration continues with impact crushers well-acclaimed for producing excellent material shape and a high reduction ratio. As the name suggests, they reduce rocks by the use of impact rather than compression. Once a rock enters the crushing chamber, it is struck by hammers fixed on a spinning rotor, which then throws the rock onto impact plates where the crushing occurs.
Delving deeper into the mechanisms of impact crushers, these machines are renowned for their versatility. Their ability to handle different types of materials – ranging from soft and non-abrasive limestone to harder granite or basalt – makes them an all-rounder in the field. Impact crushers are preferred when the shape of the final product is a crucial factor, as they yield cubic-shaped particles, a desirable trait in many industries, including construction and road-building.
3. Cone Crushers
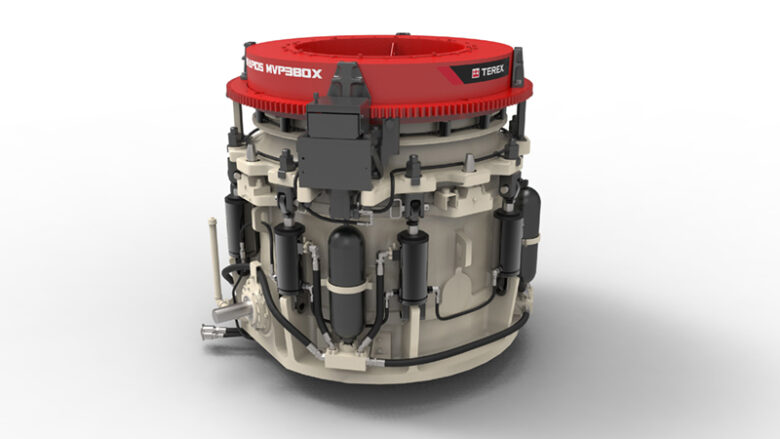
Source: terex.com
Progressing further, we delve into the world of cone crushers, characterized by their unique conical design. These primarily find their use in secondary or tertiary crushing stages. Here, the rock is placed between a fixed cone and a mobile cone that moves inside the outer one, thus breaking the rock down by squeezing and compressing it.
One cannot overlook the significant advantage that cone crushers provide in terms of product granularity. They are exceptional performers when it comes to delivering a uniform and refined output size, which is highly desired in many applications, particularly in producing aggregate for road construction. They offer varied adjustments for setting the size of the output, allowing operators to fine-tune the process as per the requirements.
4. Gyratory Crushers
Next, let’s turn our attention to gyratory crushers, the undisputed giants of primary crushing. Like their jaw crusher counterparts, they are used for heavy-duty tasks, but the distinguishing factor lies in their design. Gyratory models work on a similar principle to jaw crushers but with a circular gap. Rock is compressed between a static conical bowl and a concave mantle which oscillates about the central axis.
Peering deeper into their operations, the versatility of gyratory crushers is truly commendable. They can crush a wide range of materials of varying hardness, from soft limestone to very hard granite or basalt. This versatility, coupled with their high capacity and the uniform size of the material produced, makes them an ideal choice for high-capacity applications, such as mining and large-scale aggregate production.
5. Hammer Mills
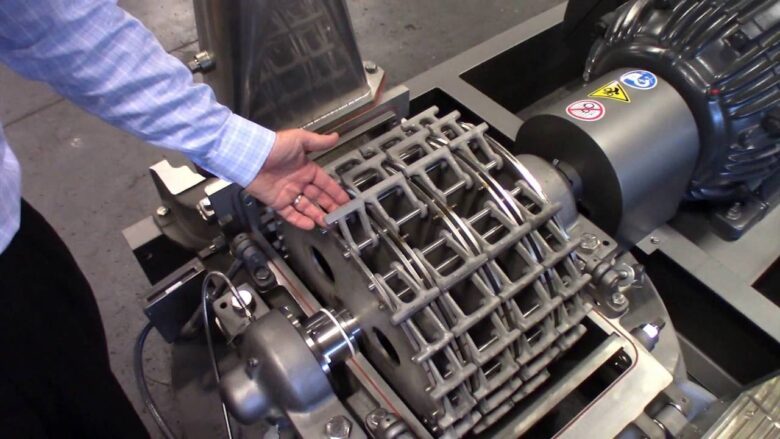
Source: youtube.com
Our sojourn brings us to hammer mills next, which are known for their versatility and high reduction ratios. In these machines, a series of hammers repeatedly strike the rocks until they reach the desired size. The smaller fragments then pass through a screen or grate designed for the required output size, making them excellent for producing finely crushed material.
Hammer mills, in addition to their versatility, are renowned for their affordability and lower energy consumption compared to other crushers. Their relatively compact size and ability to process a variety of materials make them a popular choice for smaller operations or specific applications like recycling or waste glass processing, showcasing the pivotal role they play in these industries.
6. Vertical Shaft Impact (VSI)
Coming up next are vertical shaft impact (VSI) crushers, the craftsmen of the crusher family. These crushers make use of high-speed rotors with wear-resistant tips that catch and throw the rocks against anvils or impact plates. This violent collision results in the rock breaking along its natural fracture lines, leading to a superior product in terms of shape.
Digging deeper, the remarkable characteristic of VSIs is their ability to produce a more evenly shaped product compared to compression crushers. This trait makes them particularly desirable in industries where the shape of the final product is paramount, such as in the production of sand for the construction industry. Their precision in shaping products is an attribute that sets them apart.
7. Horizontal Shaft Impact (HSI)
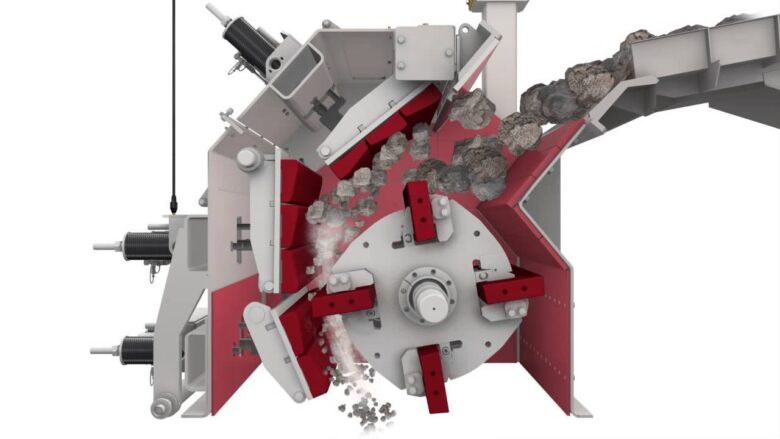
Source: indiamart.com
Transitioning to horizontal shaft impact (HSI) crushers, these machines share a common principle with VSIs – crushing by impact. However, their distinguishing factor is the horizontal shaft fitted with hammers. As the shaft rotates, the hammers hit the feed material, which then collides with fixed impact curtains or plates causing it to shatter.
It’s worth noting that HSIs excel in recycling applications and secondary or tertiary crushing of softer and medium-hard rocks. They are renowned for their high capacity and the production of a high-quality, cubical product. The ability to adjust the crushing gap allows operators to control the size of the final product, further highlighting the adaptability of HSIs.
Final Remarks
Embarking on this enlightening journey through the diverse landscape of stone crushers, we have discovered the unique features, operating principles, and applications of eight types of machines. From the robust jaw crushers to the precision craftsmen – the VSI crushers, each type contributes in its unique way to the fascinating process of stone crushing. As diverse as they are, these machines form an indispensable part of our infrastructure, playing their role in the harmonious symphony of the construction and mining industries. As we continue to build and grow, they will undoubtedly remain the linchpins of progress.