In the times we are living in almost every industry is prone to changes and what is in trend now is sure to be outdated very soon later. With this in mind, you have to keep up to date with the most effective methods and strategies of doing business. If you are a part of the manufacturing industry and metal parts manufacturing is a thing you do, deciding on the most effective methods is a must. Now, though forging and machining have been the two main methods apart from sand casting that were involved in metal manufacturing for years now we have a thing called investment casting on the rise.
The main reason for its popularity is the fact that it allows you incredible freedom and no other method can provide as versatile final elements as this one can. Along with that, it is a cost-effective option without all the limits of traditional manufacturing strategies.
Without further ado let’s go ahead and take a look at what are all the advantages of implementing investment casting in your business!
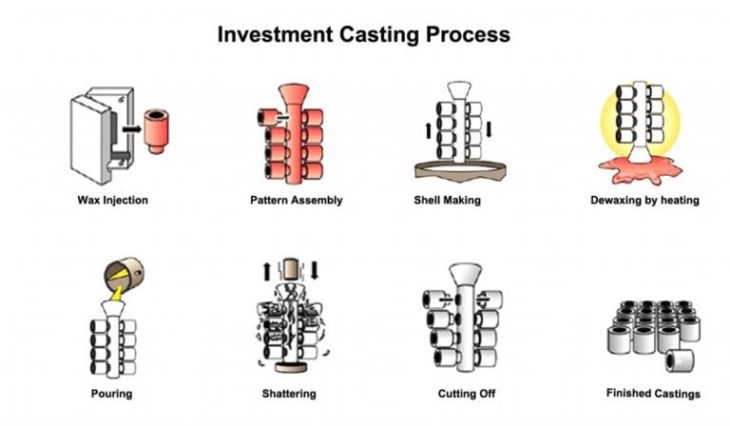
Source: Quora
The Advantages Of Investment Casting
- First and foremost and maybe the most important benefit is the fact that you have absolute freedom of design. Basically, any complex metal part no matter the pattern or dimensions will be created with ease and that for one reason – instead of forging, you are pouring liquid metal into a specific sprue that shapes the needed part. Once the time has passed and metal has solidified you will have a unique product at your hand.
- Along with that, it will not take as big of a bite at your budget as the tooling costs for investment casting are nowhere close to the ones you would spend on forging. It is more effective due to better amortization, and investment in quality tooling is sure to pay off in the course of time.
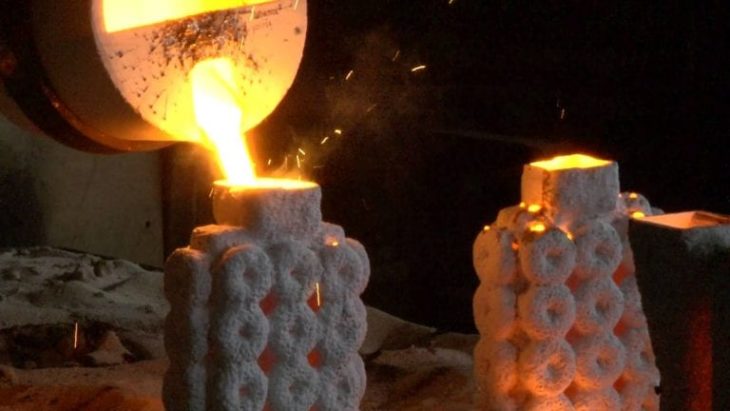
Source: Liveblogspot
- Also, the investment casting allows for a much better surface finish. While traditional methods such as sand casting or forging don’t allow for such a precise finish due to the methods used, the investment casting is much more delicate especially for the reason that no machining is included. And along with that, you will be able to get the so-called net or near net shaped metal parts with less machining job and a higher chance of meeting the CT5-CT6 standards.
- If you go for the investment casting the whole process will be at your control which in terms leads to fewer defects and more high-quality parts. This, of course, doesn’t mean that all parts will be defect-free and that is why you should carefully inspect each and every once the process is done. Still, it is much more precise and effective than other casting methods such as die or sand.
- Last but not least and for some people an absolute winner is the fact that you don’t need mass production in order to start the process. With forging it probably isn’t a worth-it investment unless you are going to make big batches due to the labor and tooling costs. On the other hand, investment casting is almost as effective if you are in need of 50-100 pcs as it is if you are planning a mass production. And that ones again goes on to show that this method doesn’t suffer from any limitations.
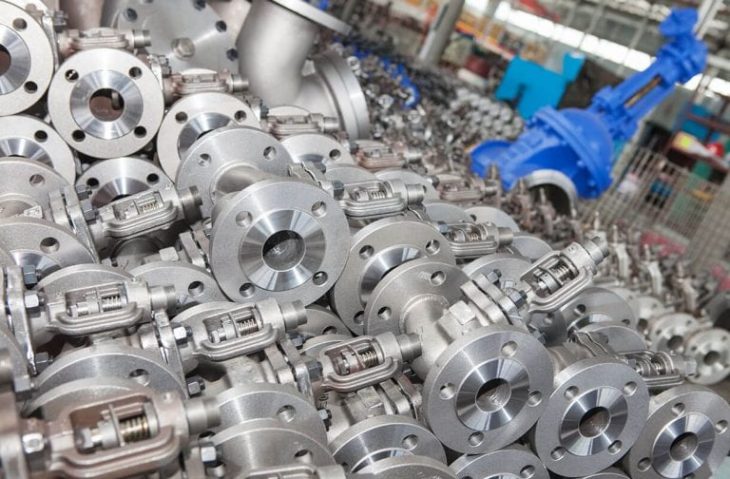
Source: Reliance Foundry
Summary
If you are in the industry that includes metal parts manufacturing you might be familiar with methods such as forging, sand casting, die casting and machining. And while these are well known and successful investment casting might still be the best one. It is cost-effective, efficient, better for the environment and versatile. If you are striving to produce specific metal parts with no design limitations than this one is your best bet!