Industrial machines known as belt press filters are used in several industries and water treatment for separating liquids from solids and can also be utilized for the production of cider, juice, and in winemaking. Since the filtration is mainly obtained by using a system of rollers through which a pair of filtering belts and cloths are passed, they are one of the key parts of the machine and play an important roll in the entire process. As such, here are some things to know about them.
Contents
What Are They?
Polyester fabric belts are circuit belt fabrics that are specifically designed for belt press filters. These mesh filter cloths are woven with high-quality monofilaments (single strands of man-made fiber) and are heat-set for stability, minimum elongation, continuous running time, flexibility, and high mechanical strength.
Since the woven filter belts determine the quality of the filtration process and the actual output, they need to have a great weave structure and be made using special yarns to achieve excellent filter cake release and rapid draining. To be able to work continuously, the belt’s ends need to be connected, with three connection types to choose from – clipper seam, spiral ring, and endless. You can check this website to learn more about this.
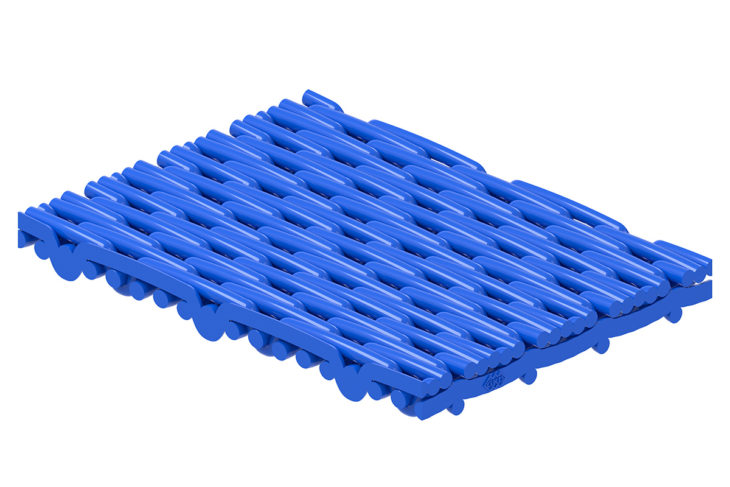
Source: GKD
Applications
These filter fabric cloths are used in several industries for separation processes of solids from liquids, particularly for the dewatering of sludges. For example, they can be utilized for wastewater and sewage treatment, the dewatering of slurry or sludge from municipal sewage plants, in the mining, chemical, and mineral industry, for the pressing and squeezing of fruits, vegetables, sugar plants, and much more.
General Features
They are extremely durable, abrasion-resistant, providing a long service life. Most are also chemically-resistant and heat-resistant, being able to withstand the temperature of up to 150 degrees. The smooth surface eases cake release and provides excellent filtration results.
Production Process
The production process includes several steps, the first being the inspection and testing of the raw material that also needs to comply with FDA and EU food contact regulations. Warping a certain number of yarns comes next, after which the weaving process begins. To improve thermal stability and ensure low elongation, heat setting is applied, and then the edges are cut using heat to make them flat, straight, and firm. Fixing the clipper seam or making the other connection types and sealing the edges with resin glue is the last step before the filter belts are packaged in rolls and place on either wooden pallets or wooden cases, or in poly-woven bags.
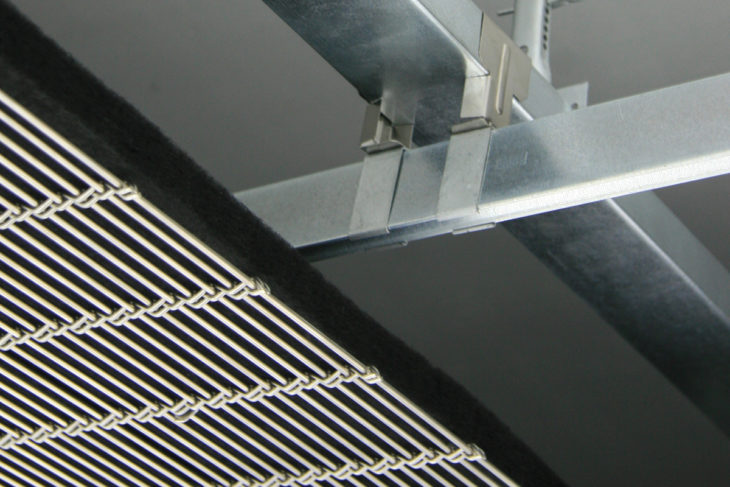
Source: GKD USA
What to Consider When Choosing
There are several factors to consider to choose the right filter cloth for your belt press filters. Depending on the industry, choose the suitable material for your belt. Pick one that offers optimal air permeability, and choose the weave type that best fits your needs. Joint and edges treatment are always the weakest parts of the filter belt, so choose the connection type carefully. Stainless steel clippers are best for most processes so that they might be the optimal solution.
Conclusion
These filter belts are extremely versatile and come in various patterns, allowing them to meet a vast range of requirements from filtering, dewatering, drying, and many more. Their quality provides an extensive running time while providing strength and stability in the process as well, so make sure to always buy from a manufacturer that is professional and reliable.