Like everything else nowadays, the advances in metal finishing technology help various businesses with being more efficient, as well as earning higher revenue. A new innovation can easily make a big difference in the metal finishing industry, which is why you might have started wondering, what those advancements are.
And if you are in this situation, you should know that this article might help you quite a lot. The text below is going to feature a list of 8 advances made in the metal finishing industry. Let’s take a closer look:
Contents
- 1. Improvements in Nanotechnology
- 2. Machines That Can Deburr And Polish Items And Surfaces
- 3. Chemistry is Getting Improved Daily
- 4. Non-Metal Enzymes
- 5. The Implementation of Dry Processes
- 6. Thickness Gauge Measures
- 7. Machines For Reducing Solvent Waste
- 8. Anodic Powder Coating For Better Anodizing Aluminum
1. Improvements in Nanotechnology
This incorporates several processes including technological, scientific, as well as engineering at a nanoscale, which means that it is close to one to one-hundred nanometers. Nanotech will have a major influence on the metal finishing industry, especially since the small crystalline metals are more strong & durable, tear-resistant, and rust-resistant when compared to other surfaces.
Additionally, the crystalline is also lighter, which means that the item can be easily transported, as well as stored in your manufacturing facility. Also, you won’t be required to add several thin coats to protect the item properly, instead, you’ll only need one layer.
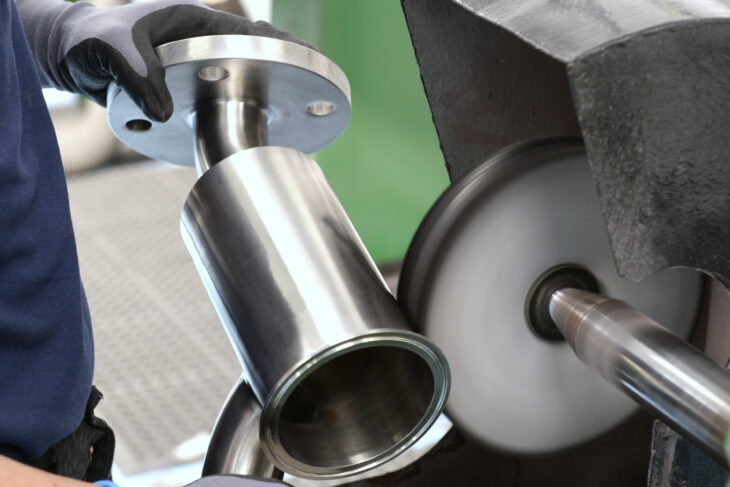
Source: axiumprocess
2. Machines That Can Deburr And Polish Items And Surfaces
There are various companies such as Shiny Smooth that offer innovative techs such as vibratory finishing machine that can be used for deburring and polishing different items and surfaces. It comes in a wide range of sizes – most commonly from 25 to 1.200 liters, and they are easy to implement and maintain.
They are suitable for various processes including jewelry and huge engine housing, it is durable, and it features a heavy-duty motor that is quite durable and strong. If you are interested in learning more about these innovative machines, you can click here for additional information.
3. Chemistry is Getting Improved Daily
Derived by rising customer demands, as well as strict regulations imposed by governments, metal finishing processes are slowly moving away from dangerous substances and chemicals and utilizing chemicals that are safer for both the consumers and our environment.
Although the innovations in this particular science field are advancing slowly, we can expect new methods in the next few years. Nonetheless, you should keep an open eye for these innovations, especially since implementing them can make your company more green and Eco-friendly.
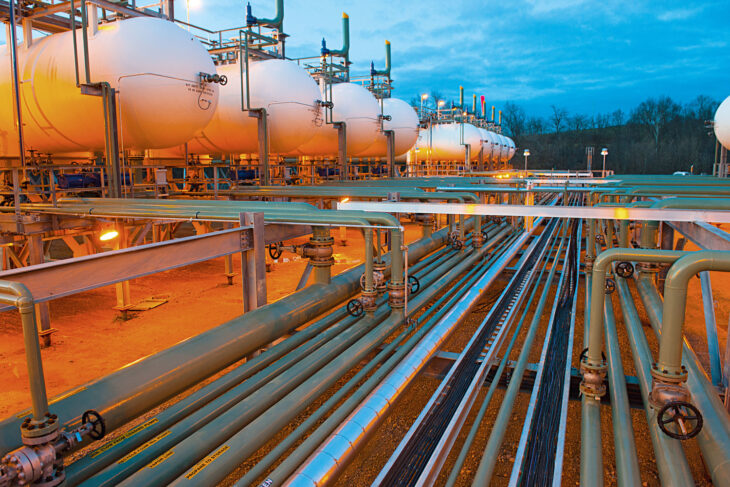
Source: briccomf
4. Non-Metal Enzymes
As you already know, metal is the main electroplating enzyme. The objective of electroplating tech is to create a substrate that does not contain any metals. This is why a lot of scientists are working on composite substances that won’t have metal with reinforcements made from glass, carbon, as well as Kevlar.
Hence, we are seeing increased use of substrates that are more durable and stronger, which means that they can last longer and that they are resistant to corrosion, and wear & tear. Hence, in the long run, you can save a lot of money because you won’t need to add extra layers to make the surface stronger.
5. The Implementation of Dry Processes
If you have been in the metallurgy industry for some time, you are probably aware that most plating processes utilize wet surface finishing processes. Well, recent trends do show the potential for the widespread use of dry processes for finishing. In return, it can reduce the production of harmful industrial waste and the use of hazardous chemicals and substances. This will be one of the biggest steps in making the entire industry environmentally friendly and overall greener.
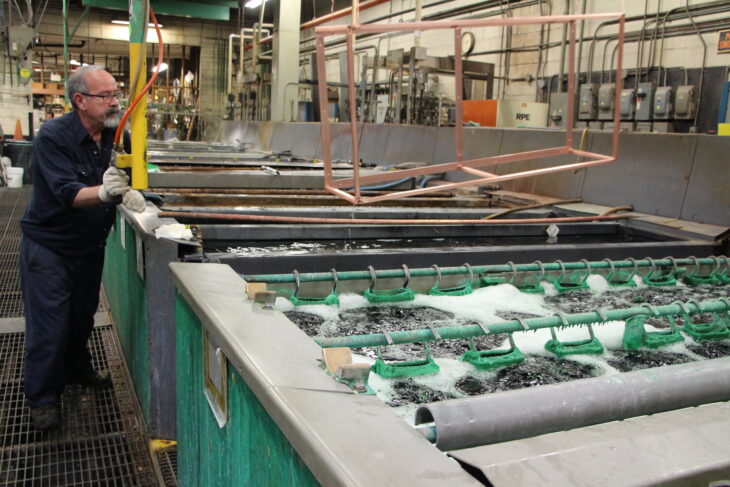
Source: sunpolishing
6. Thickness Gauge Measures
This device is a powder & liquid coating thickness gauge is manufactured to effortlessly measure both powder and dye finishes up to one thousand microns on smooth metal surfaces. This means that the manufacturing company can meet their clients’ needs, specifications, and requirements.
The layer thickness does not only revolve around appearance. If there is too much paint in one location, for example where the bolt of screw needs to be attached, the thickness of the dye will hinder the workers from inserting and attaching those items, which means that it can easily affect the overall performance.
7. Machines For Reducing Solvent Waste
The dosing and mixing system is created for the difficult and daunting application of several colors. Most commonly, the machines can process more than 25 colors, as well as 4 parts at the same time. Additionally, it allows color changes in less than a minute, which means that you can cut down the production time.
There is one interesting thing about such systems – they can easily and automatically adapt to different working environments, which means that you won’t need to worry about adjusting it every time. Also, it can preserve approximately 90% of solvents when the color is changed.

Source: siaabrasives
8. Anodic Powder Coating For Better Anodizing Aluminum
You already know that low abrasion and bad colors affect the overall quality of your product, and in the end, it will impact your product amount as well, which is something that can easily lead to your company losing a lot of money. But, there is something that can help with this.
The aluminum field has traditionally utilized anodized substances for manufacturing processes, however, various companies are now hoping for the widespread use of anodic powder. So, this means that the coating will look like aluminum that was anodized, however, it will be better than it. This can increase the overall customer satisfaction levels and it will certainly improve your revenue.
Before we conclude this article, you should keep in mind that the things mentioned in the article above are only some of the hundreds of new innovations. This means that you can do a bit more digging and learn what other things you might be looking forward to implementing in your business.
Conclusion
As you can see, there is a wide range of technological innovations in the metal surfacing industry. Of course, you won’t need to implement every single one mentioned above, instead, it is best if you choose one that will suit your business needs, as well as requirements.
So, now that you know what are some of the top advancements in this field, you should really not waste any more of your time. Instead, determine what your budget is, and start browsing online and brick-and-mortar businesses in order to find what you are looking for.