When it comes to motion control, feedback is crucial. Encoder feedback is influenced by servo motors and stepper motors to regulate speed and position exactly. An encoder is a type of transducer that turns the movement of a tracked item, like a motor shaft or a weight, into an analog or digital production that adapts to acceleration or position.
Encoders are high-end feedback equipment, but only when the application is defined in a suitable way with the possible circumstances. For more information related to the right motion feedback solution for your application, it is best to check out Encoder.com. Here, you can find different types of motion feedback solutions.
Contents
Getting The Right Motion Feedback Solution For Your Application
Here, we will have a look at different types of motion feedback solutions that are suitable for various applications. With that, it will be easy for you to choose and acquire the right motion feedback solutions.
Optical Encoders
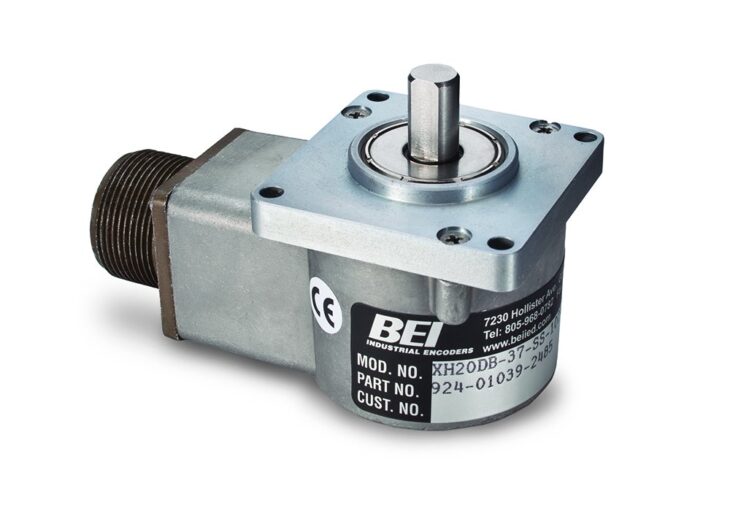
Source: amazon.com
In the optical encoders, there will be a figured disc connected to the item, which is monitored, and it departs through a source and a photodetector present on the encoder’s body. The styling of the disc slices the shaft to produce a series of square wave beats or create a binary digital term. In both situations, the management utilizes the information to assume the position and perhaps velocity.
As for a linear optical encoder, the source and sensor operate with the weight. In addition to that, the linear scale produces the outcome and is attached to the device rack. Optical encoders are suitable for industrial and scientific applications in which relatively rigorous output performance is needed.
These encoders give the elevated outcome of this class of feedback appliances. Besides that, you can use them for applications that need tracing angular posture to the rule of fractions of grades. However, optical encoders are vulnerable to deterioration, and you can not utilize them for applications that get in touch with dirt, water, or other corrosive chemicals.
Magnetic Encoders
If you are looking for ideal motion feedback solutions for industrial applications in severe environments, it is best to consider magnetic encoders. They perform correspondingly to the above-listed optical encoders. These encoders have a magnetic rotary that utilizes a distinct configuration to disturb the magnetic area, like drums, toothed ferrous metal equipment, discs figured with rotating magnetic spaces.
You have to keep in mind that linear editions utilize linear scales. The magnetic encoders have the potential to resist relatively severe circumstances. Due to that, they are best suitable for various industrial applications. These motion feedback solutions can work even if they are exposed to dirt, moisture, and high vibrations.
Another best part about them is that they are accessible at an affordable price. The magnetic encoders are vulnerable to elevated magnetic fields and might need protection. There is a chance that massive shock pressures can degauss the magnetic domains.
Inductive Encoders
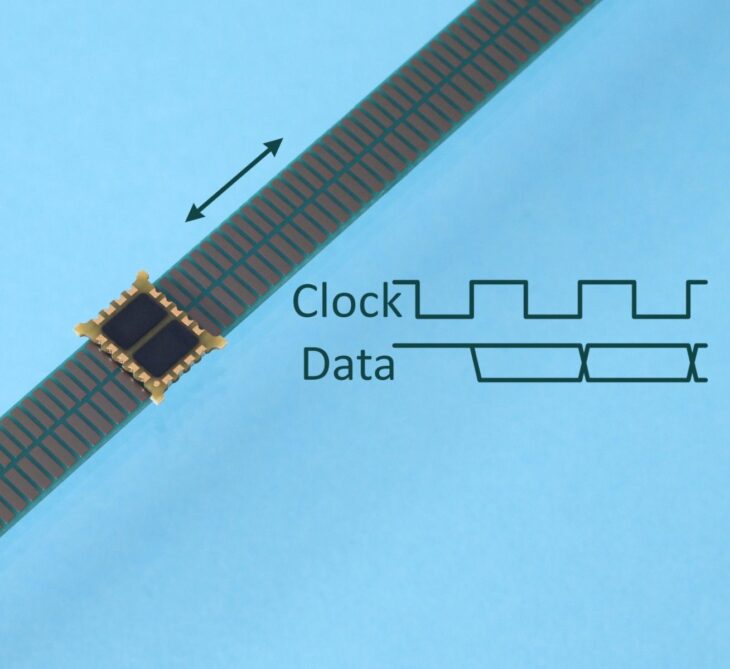
Source: posic.com
Next, we have inductive encoders, which are almost connected to resolvers. They are distinct transformers determining the ultimate angular posture of the rotating load by tracing the voltages caused in a set of readout loops. The central coil is bound to the rotor and stimulated, and the minor sine and small cosine loops are connected to the stator.
The inductive encoders are reliable enough to resist impurities, fluid ingress, severe climatic conditions, shock, and vibrations. They are portable and easy to use. Despite the inductors being durable, there is a possibility that conductive disks can develop problems. It is vital to choose a suitable conductive disk. These types of feedback motion solutions are the best choice for applications that deal with harsh circumstances and have a need for high resolution or precision.
Absolute Encoders
The absolute encoders are accessible in several models in order to match the various types of applications. You can find multi-turn and single-turn absolute encoder solutions, and numerous models come with a maintenance-free and eco-friendly magnetic configuration. A few models are made using energy harvesting magnetic multi-turn technology. They do not possess or require any batteries or gears.
It is best to choose the absolute encoders which fulfill the CE or EMC criteria for protection and emissions. They give maintenance-free feedback and are ideal for absolute applications. You can also use them for applications where it is vital to conserve the position data after the loss of system energy.
Incremental Encoders
An incremental encoder is an electro-mechanical device that uses an optical disc to convert the angular position of the shaft into digital or pulse signals. Per revolution, a specified number of pulses are created, each of which represents an increase matching to the interpreted resolution. The absolute position can not be assessed with an incremental encoder because it can only estimate the difference in position.
The pulse is measured from zero when the incremental encoder is turned on. It means the position is not saved, and the reset or reference posture has to be established prior to the following counting of the encoder. There are several benefits of incremental encoders: they are affordable, less complicated, come with high noise immunity, and more.
Linear Encoder
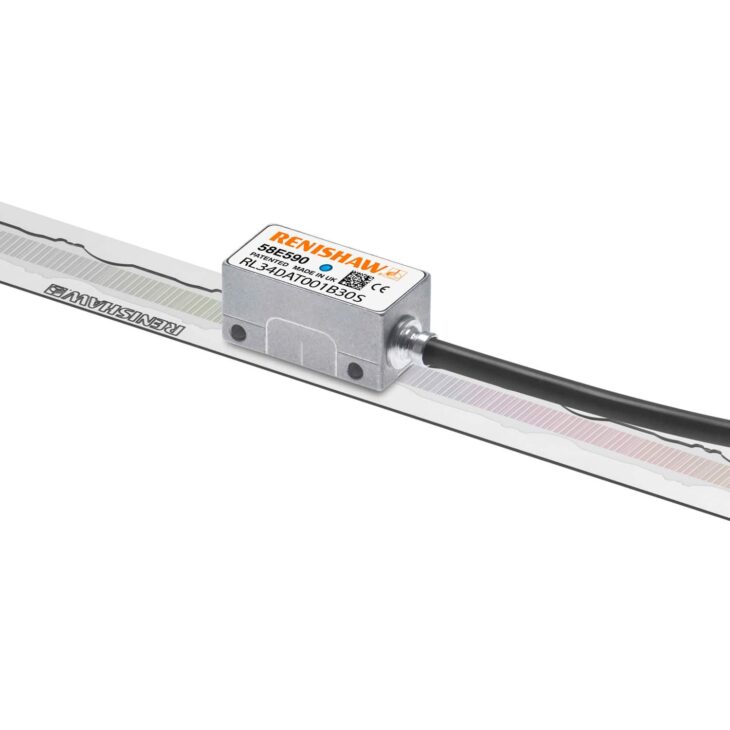
Source: directindustry.com
Coming to the linear encoder, it is a sensor, transducer, or readhead partnered with an order that encrypts position. Then the sensor examines the order to restore the encoded posture into a digital or analog signal. Later on, it can be analyzed into position using a motion controller or digital readout.
There are about two primary areas of applications for linear encoders. The first one is measurement applications, which comprise digital readouts, calipers, coordinate-measuring appliances, tension testers, laser scanners, and several others. Motion systems are another type of major application for linear encoders. They include machine tools, wire bonders, digital presses, robotics, and more.
Bottom Line
Defining an encoder begins with the necessities of the application. You need to consider a few aspects: environmental circumstances, kind of motion, electrical needs, the magnitude of the action, sensitivity, mechanical design, manual format, and cost. Depending on the type of your application, you can get the right and ideal motion feedback solution.