For more than 60 years, zeolite molecular sieves are often used in biotechnical industrial applications. Mostly as very efficient adsorbents for gas or liquid phase separation operations. Zeolite molecular sieves can be used in powder form, especially in static implementations. But they can also be used as shaped material in both static and dynamic (flowing media) applications to a much greater extent.Over the last few decades, many molecular sieve shaping methods have been created for biotechnology. As a result, the various requirements for molecular sieves in various applications are reflected. In the field of Biotech, more specific, tailor-made forms of zeolite molecular sieves are required due to new market problems.New types of zeolites or zeolite-like materials are used by molecular sieve manufacturer firms to reach this level of specificity. Modified synthesis and/or post-synthesis treatments, as well as tailored shaping techniques to the application’s requirements. Click here for more information.
Let’s take a look at how molecular sieves are bringing innovation to the Biotechnology world.
Contents
Major Applications
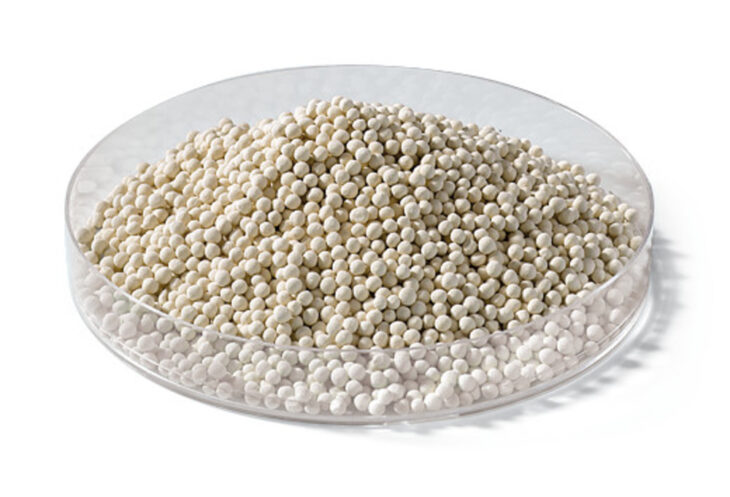
Source: carlroth.com
In the petroleum industry, molecular sieves are frequently used, particularly for drying gas streams. For example, in the liquid natural gas (LNG) business, the water content of the gas needs to be decreased to less than 1 ppmv to prevent obstructions produced by ice.
To dry the solvent in the lab, molecular sieves are as important as the mig welding robot in assembling labs. Traditional drying processes, which often use strong desiccants, have proven to be inferior to “sieves.”
Molecular sieves are referred to as zeolites and are employed in a variety of catalytic applications. They are employed in large-scale industrial processes such as hydrocracking and fluid catalytic cracking to catalyse isomerization, alkylation, and epoxidation.
They’re also utilised to filter air supply for breathing apparatus used by scuba divers and firefighters, for example. The air is provided by an air compressor and then passed through a cartridge filter packed with molecular sieve and/or activated carbon, depending on the application, before being used to charge breathing air tanks.
This form of filtering can remove particulates and compressor exhaust products from the breathing air supply.
Biotech Regeneration (Activation)
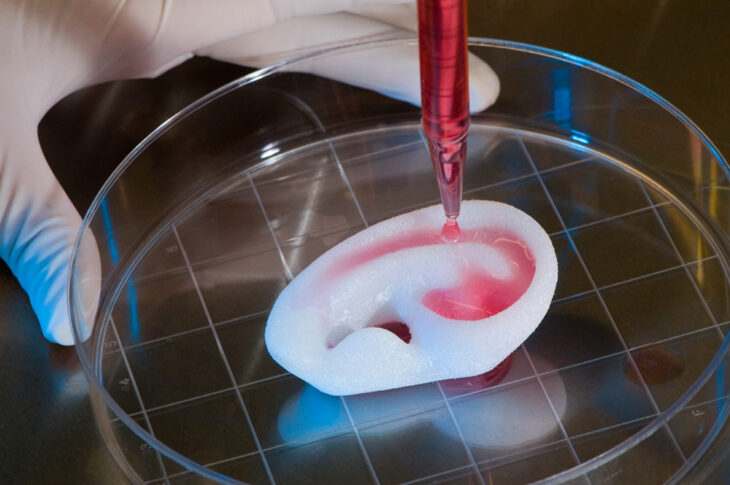
Source: pharmaceutical-technology.com
In typical cycle systems, regeneration entails heating and purging with a carrier gas to remove the adsorbate from the molecular sieve bed. To vaporize the liquid and offset the heat of wetting the molecular sieve surface, enough heat must be applied to raise the temperature of the adsorbate, the adsorbent, and the vessel.In Biotech regeneration, the temperature of the bed is crucial. For type 3A, bed temperatures in the 175-260° range are commonly used. When olefins are present in the gas, this lower range reduces the polymerization of olefins on the molecular sieve surfaces. Most olefinic materials will be removed at low temperatures, so slow heat is recommended; temperatures in the 200-315 °C range are required for 4A, 5A, and 13X sieves.
A cooling interval is required after regeneration to bring the molecular sieve temperature down to within 15° of the temp of the stream to be treated. The most convenient way to do this is to use the same gas stream as is used for heating but with no heat input.
During the heat-up cycle, the gas flow should be countercurrent to adsorption, and during the cooling cycle, it should be concurrent (relative to the process stream). Small quantities of molecular sieves can also be dried in the absence of a purge gas by heating them in an oven and then cooling them slowly in a closed system like a desiccator.
Types of Molecular Sieves Used in Biotech Labs
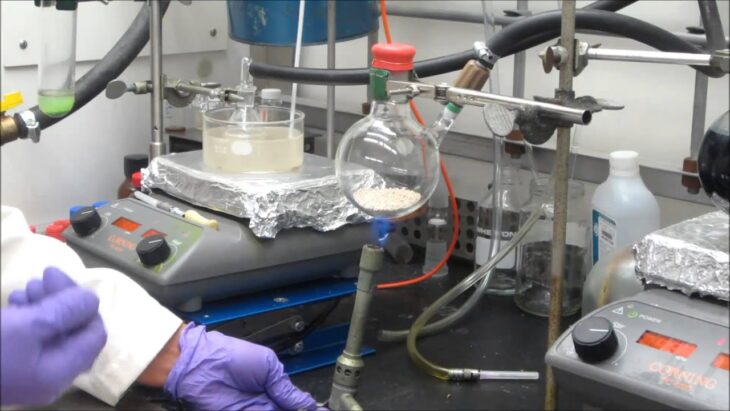
Source: dir.indiamart.com
Molecular sieves come in a variety of forms and sizes. However, spherical beads have an advantage over other shapes in that they have a lower pressure drop, are degradation resistant due to the lack of sharp edges. They are strong, requiring a larger crush force per unit area. Because certain beaded molecular sieves have a lower heat capacity, they require less energy during regeneration.Another advantage of employing beaded molecular sieves is that their bulk density is usually higher than that of other shapes, requiring less molecular sieve volume for the same adsorption demand. As a result, beaded molecular sieves can be used to de-bottleneck, allowing more adsorbent to be loaded into the same volume while avoiding vessel alterations.
The following are examples of molecular sieves used in various industries:
- 3Å molecular sieves have been used to dry ethanol, air, refrigerants, natural gas, and unsaturated hydrocarbons, among other things. Cracking gas, acetylene, ethylene, propylene, and butadiene are among the latter. To extract water from ethanol, a molecular sieve is used.
- Drying laboratory solvents with 4Å molecular sieves is a common practice. It’s frequently utilised in liquid and gas drying, refining, and purification (such as the preparation of argon).
- In the petroleum sector, five ngström (5) molecular sieves are frequently used, particularly for the filtration of gas streams. Drying natural gas, as well as desulfurization and decarbonization, is done using five angström molecular sieves.
Conclusion
The global zeolite molecular sieve market is primarily driven by the rising demand for high-performance catalysts in the Biotech industry. The growing demand for effective water treatment systems is fueling market expansion.Furthermore, because zeolite molecular sieves are employed as a binding agent in liquid and powder substances, market growth is aided by rising sales of items such as soaps and detergents. Moreover, constant product improvements, such as silver-infused sieves with antibacterial qualities, are enhancing the market’s favourable outlook.