Plastics are the most used material in manufacturing home appliances and other different household essentials. Plastics fall in the resilient material category, with hundreds of polymer alternatives and unique mechanical characteristics. But how are these plastic appliances manufactured?
Thus, numerous plastic manufacturing techniques have been developed to meet various applications, designs, and plastic types. However, it is vital for every designer or engineer working and the plastic home appliances manufacturers in product development to be knowledgeable about today’s manufacturing alternatives and the new advancements that indicate how components will be manufactured in the future. Click to find out more.
Thus, this article includes an overview of the most popular plastic appliances manufacturing processes and tips to help you choose the best solution for your application.
Contents [show]
Choosing the suitable plastic for Manufacturing Process
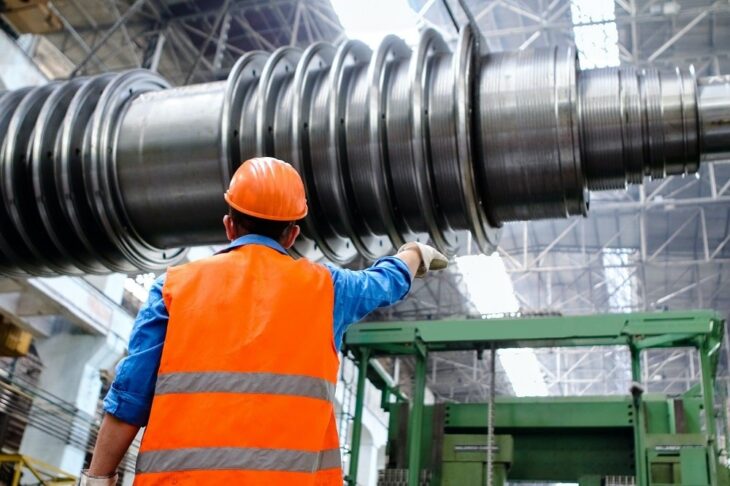
Source: techonthego.co.uk
When selecting a manufacturing process for your product, keep the following aspects in mind:
Form
Do your items demand strict tolerances or have complicated interior features? Manufacturing alternatives may be restricted depending on the geometry of a design, or it may require extensive design for manufacturing optimization to make it cost-effective to create.
Volume/Cost
What is the total or yearly amount of components that you want to manufacture? Some manufacturing techniques involve substantial upfront tooling and setup costs yet generate low-cost components on a per-part basis. Cheap-volume manufacturing techniques, on the other hand, have low beginning costs. Still, because of longer cycle times, less automation, and human labour, the cost per item remains constant or only slightly lowers as volume grows.
Lead time
How fast do you require components or completed goods? Some procedures produce initial pieces in as little as 24 hours, while others require months of tooling and setup for high-volume production.
Material
What kinds of pressures and strains will your product have to withstand? A variety of factors influence the selection of the best material for a particular application. Moreover, the cost of manufacturing the product is weighed against the applicable criteria.
You should also consider the suitable features for your application and compare them to the options accessible in a particular production process.
Types of Manufacturing Processes
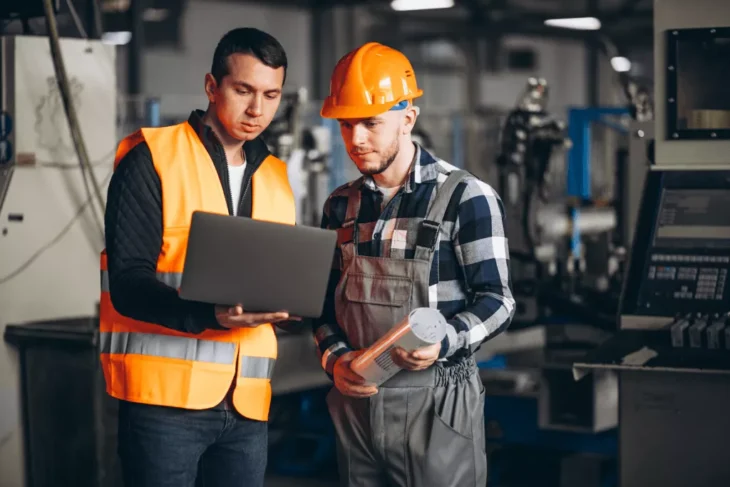
Source: corningdata.com
Various processes can be followed while manufacturing plastics:
Injection Molding
Injection moulding (IM) is when molten thermoplastic is injected into a plastic injection mold. It is the most extensively utilized method for producing plastic components in large quantities.
Injection molding molds are incredibly intricate and must be manufactured to stringent requirements to generate high-quality goods. Because of the high temperatures and pressures necessary, these moulds are built of metals such as hardened steel. Softer aluminium moulds are less expensive, but they wear out more quickly. As a result, they are frequently used for smaller manufacturing runs.
Injection molding, despite its high beginning costs and sluggish ramp-up, is unrivalled for high-volume applications. Cycle times are only a few seconds once the tooling is up and running. Millions of high-quality components may be produced for a fraction of the cost of traditional production procedures.
3D Printing
The cost of manufacturing plastic home appliances is insignificant compared to traditional manufacturing procedures since 3D printers require no tooling and minimal setup time for a new design.
3D printing procedures are often slower and more labour-intensive than mass-production manufacturing processes. As 3D printing technology advances, the cost per appliance decreases, allowing for a more extensive range of low- to mid-volume applications.
While traditional plastic manufacturing procedures need costly industrial gear, dedicated facilities, and expert operators, 3D printing enables businesses to make plastic components and prototypes in-house quickly.
CNC Machining
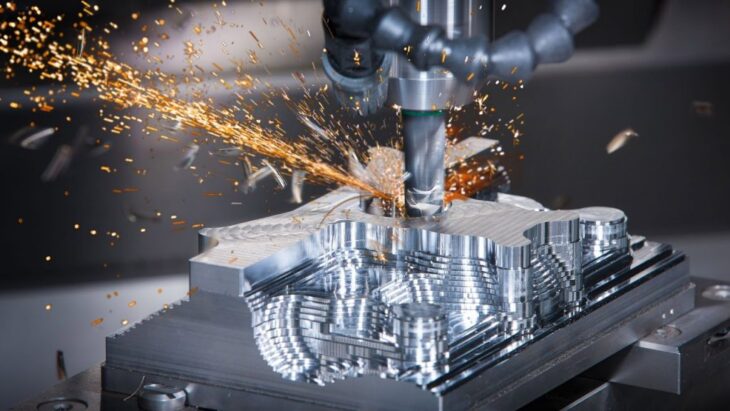
Source: cymanufacturing.com
Mills, lathes, and other computer-controlled subtractive operations are examples of CNC machining. These procedures begin with solid metal or plastic blocks, bars, or rods formed by removing material by cutting, boring, drilling, and grinding.
Moreover, unlike most other manufacturing processes, CNC machining is a subtractive process. In this method, the raw material is removed using either a spinning tool and a fixed component (milling) or a spinning part and a fixed tool (lathe). Furthermore, CNC machining has low to moderate setup costs and can quickly manufacture high-quality plastic products from various materials.
Polymer Casting
A reactive liquid resin or rubber is poured into a mold in polymer casting, which reacts chemically and solidifies. Polyurethane, epoxy, silicone, and acrylic are common casting polymers.
Polymer casting is low-cost and requires little initial investment, but thermoset polymers are often more expensive than their thermoplastic counterparts, and molding cast components is time-consuming. Post-processing of each cast item necessitates manual effort, resulting in a higher final cost per part than automated manufacturing processes like injection molding.
Rotational Molding
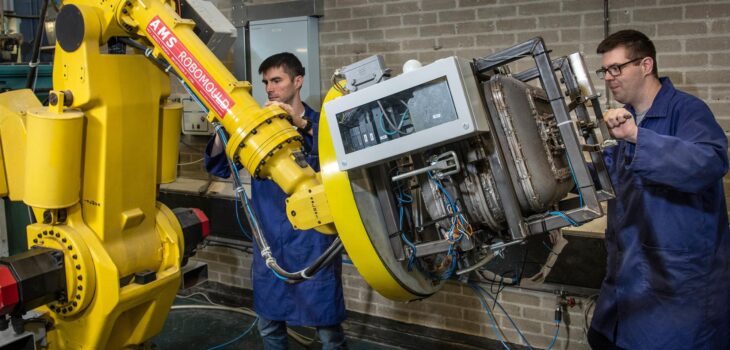
Source: qub.ac.uk
Rotational molding (also known as roto-molding) produces hollow things by heating an open mold filled with powdered thermoplastic and rotating it along two axes. Thermoset polymers may also be rotomolded, albeit this is a less usual process.
Because the procedure employs centrifugal force rather than pressure to fill the mold, rotational molding requires less expensive tooling than other molding processes. Moreover, with this method, molds for great products can be created, such as CNC machined, cast, or constructed from epoxy or aluminium, at a lower cost and much faster than tooling for conventional moulding techniques.
Appliances produced by rotomolding have approximately homogeneous wall thickness. Once the tools and procedure are in place, the cost per component is relatively low compared to the part’s size. Prefinished elements, such as metal threads, internal pipes, and structures can also be added to the mold.
Wrapping Up
Plastic Home Appliances have become the necessity of every household these days. People only prefer the appliances and products they stay longer, and thus, it all depends on the manufacturing process of the products. If you have read the article thoroughly, you must know the best method for manufacturing plastic products.
However, talking about personal opinion, injection molding is at its peak these days because of the high-quality results that it offers. Thus, it would be best if you also consider this option at least once.