Contents
- Understanding Push Back Racking and Its Importance in Warehouse Operations
- The Benefits of Push Back Racking Dimensions for Maximizing Storage Capacity
- Exploring Different Types of Push Back Racking Systems and Their Unique Features
- The Factors to Consider When Determining the Ideal push back Racking Dimensions for Your Warehouse
Understanding Push Back Racking and Its Importance in Warehouse Operations
What is pushback racking? Push back racking is a storage system that plays a crucial role in warehouse operations. It is designed to maximize storage space while promoting efficient inventory management. This system allows for high-density storage, making it ideal for warehouses with limited space. In push back racking, pallets are stored on wheeled carts that flow on inclined rails. As new pallets are loaded, they push the existing ones back, hence the name “push back” racking. This arrangement allows for easy access to multiple pallets and ensures FIFO (First-In, First-Out) inventory rotation. Now, let’s delve deeper into the importance of push back racking in warehouse operations.
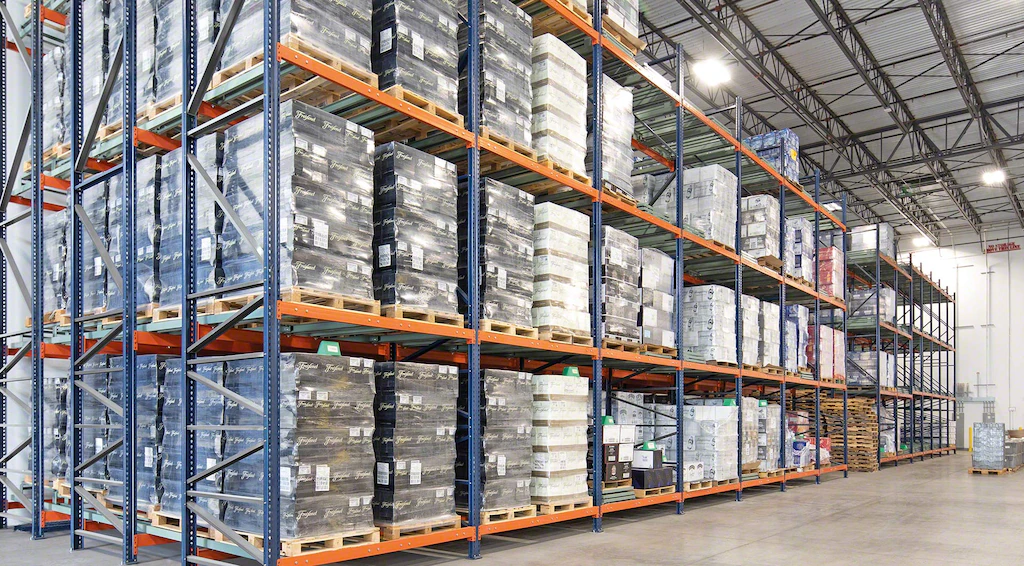
Source: interlakemecalux.com
The Benefits of Push Back Racking Dimensions for Maximizing Storage Capacity
Push back racking is a popular storage solution that offers numerous benefits for maximizing storage capacity. One key advantage is its ability to optimize available space by utilizing both depth and height. By allowing for high-density storage, push back racking dimensions can help businesses make the most of their warehouse or storage facility.
Here are some specific benefits of push back racking dimensions for maximizing storage capacity:
- Increased Storage Density It allows for the storage of multiple pallets in a single lane, providing higher storage density compared to traditional selective racking systems. This means that more products can be stored in the same amount of space, making it an efficient solution for businesses with limited space.
- Time and Space Efficiency: With this, pallets are loaded and unloaded from one side only, eliminating the need for multiple aisles. This saves both time and space, as forklifts can easily access the desired pallet without having to navigate through multiple lanes. It enables faster loading and unloading processes, resulting in increased productivity.
- FIFO (First-In, First-Out) Inventory Management: It operates on a Last-In, First-Out (LIFO) principle, allowing for efficient inventory management. The system works by using a series of inclined rails and carts that move each pallet forward as an item is loaded or unloaded. This ensures that the oldest stock is accessible first, reducing the risk of product expiration or obsolescence.
- Versatility and Flexibility: It can accommodate various pallet sizes and weights, making it a versatile option suitable for different industries and products. The system can be customized to meet specific storage requirements, allowing businesses to adapt the rack dimensions based on their needs.
- Safety Considerations: This system is designed with safety in mind. They typically feature features such as safety stops and speed controllers to prevent accidents during loading and unloading. Additionally, the inclined rails and carts are designed to support the weight of the pallets, ensuring stability and preventing product damage.
Push back racking dimensions offer several benefits for maximizing storage capacity. With increased storage density, time and space efficiency, FIFO inventory management, versatility, and safety considerations, it is a reliable solution for businesses looking to optimize their storage space and improve operational efficiency.
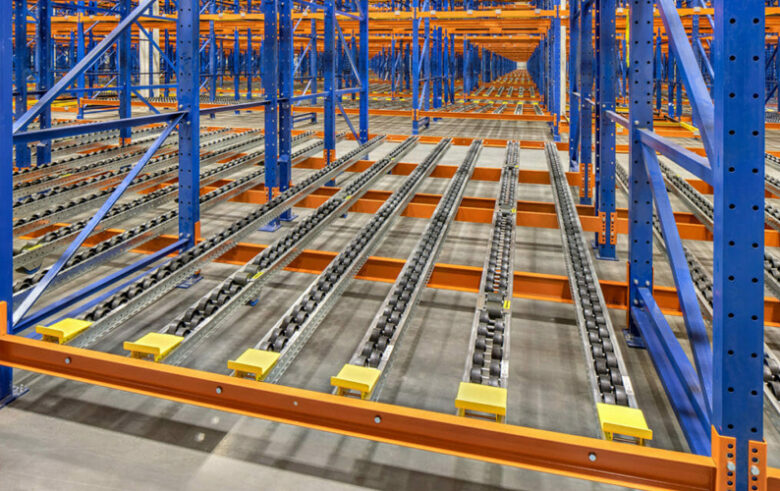
Source: atlanticrack.com
Exploring Different Types of Push Back Racking Systems and Their Unique Features
Push back racking systems are a popular choice for warehouse storage due to their high density and efficient use of space. These systems utilize a series of nested carts that are loaded and unloaded from one side, allowing for the storage of multiple pallets deep.
There are several different types of push back racking systems, each with its own unique features and benefits. Let’s explore some of these types:
- Single Lane: This type consists of a single lane of carts, where each cart is loaded with pallets and pushed back into the rack. When unloading, the first pallet is removed, causing the other pallets behind it to roll forward for easy access.
- Double Lane: With double lane push back racking, two lanes of carts are stacked on top of each other. This configuration allows for increased storage capacity while still maintaining the ability to load and unload from one side.
- Gravity Flow: In gravity flow push back racking, the carts are equipped with rollers or wheels that allow them to glide smoothly along inclined tracks. This design ensures that pallets move forward automatically when one is removed, making the unloading process faster and more efficient.
- Pallet Flow: Pallet flow push back racking combines the benefits of both push back and pallet flow systems. The carts are equipped with rollers or wheels and are placed on a sloped track. As pallets are loaded from one side, they automatically flow towards the unloading end due to gravity.
- Hybrid: Hybrid push back racking combines different storage methods within a single system. For example, it can incorporate a combination of single lane push back, double lane push back, or even selective racks depending on specific storage requirements.
Each type of push back racking system offers its own advantages, depending on factors such as storage capacity, accessibility, and efficiency. It’s essential to consider the specific needs of your warehouse before selecting the most suitable option.
Remember to consult with a professional racking supplier or warehouse consultant to ensure the right type of push back racking system is chosen for your specific requirements.
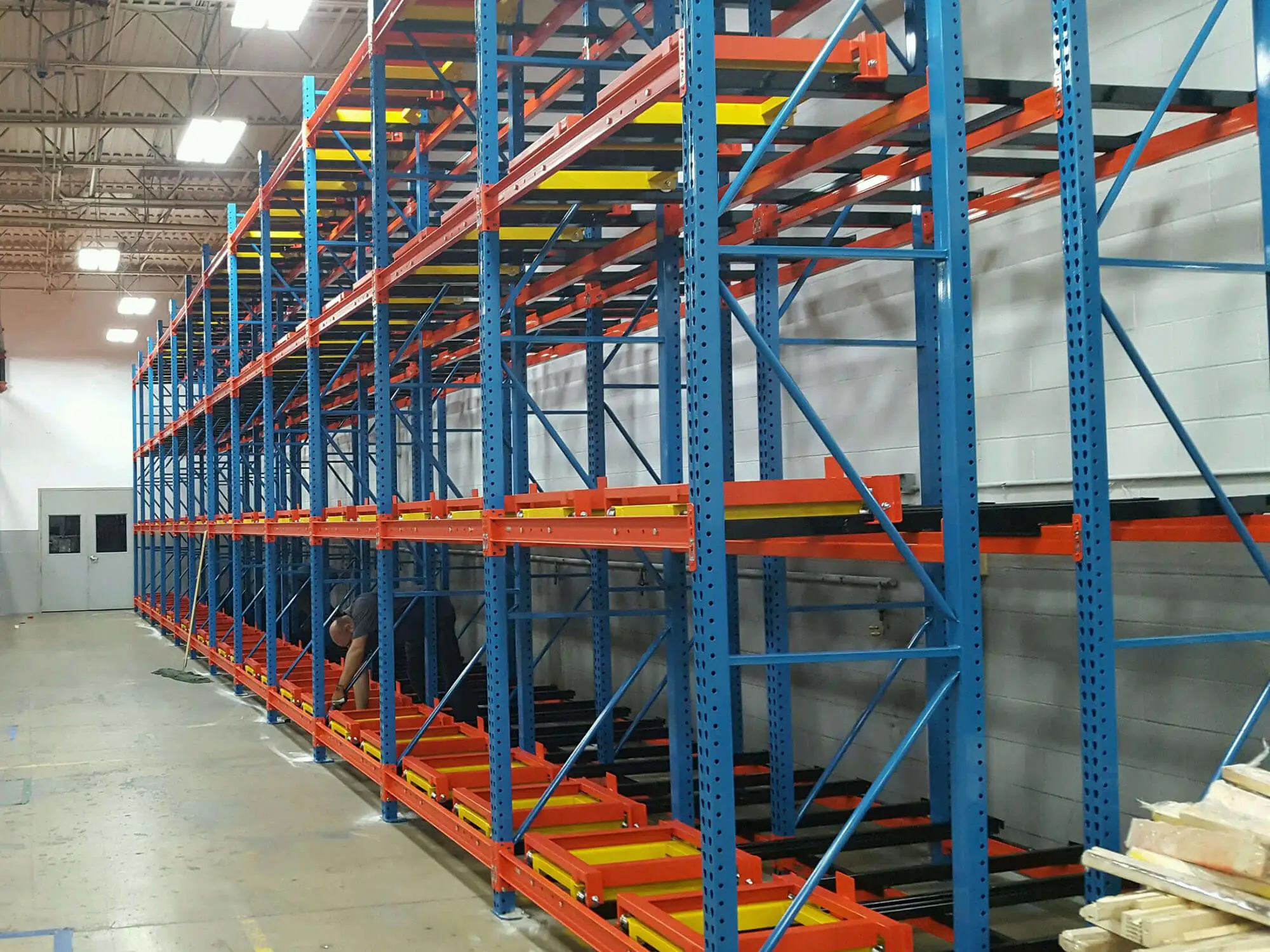
Source: chinastoragerack.com
The Factors to Consider When Determining the Ideal push back Racking Dimensions for Your Warehouse
When determining the ideal push back racking dimensions for your warehouse, there are several factors that you should consider. These factors will help ensure that the push back racking system you choose is suitable for your specific needs and maximizes the use of available space. Here are some key considerations:
- Available Space: Evaluate the dimensions of your warehouse, including ceiling height, floor space, and aisle widths. This will help determine the maximum height and depth of the push back racking system that can be installed.
- Load Capacity: Consider the weight and size of the products or pallets you will be storing on the push back racking system. Ensure that the dimensions of the racking system can support the expected load capacity to avoid any safety or structural issues.
- Accessibility: Assess how often you will need to access each pallet or load. push back racking allows for Last-In-First-Out (LIFO) inventory management, meaning that accessing items from the front of the rack is quicker and easier. Consider if this accessibility is important for your warehouse operations.
- Forklift Compatibility: Determine what type and size of forklifts will be used in your warehouse. The dimensions of the push back racking system should allow for safe and efficient loading and unloading by your specific forklifts.
- Storage Density: Evaluate how much storage density you need in your warehouse. push back racking systems offer higher density storage compared to traditional selective racking systems, as they allow multiple pallets to be stored in a single lane. The depth of the system will determine how many pallets can be stored.
- Safety Regulations: Ensure that the push back racking system complies with local safety regulations and industry standards. This includes considering factors such as fire safety, weight distribution, and stability.
- Future Expansion: Take into account any future growth or changes in your inventory management needs. Leave room for potential expansion or modifications to the push back racking system, if required.
By considering these factors, you will be able to determine the ideal push back racking dimensions for your warehouse, leading to efficient storage and optimized operations.
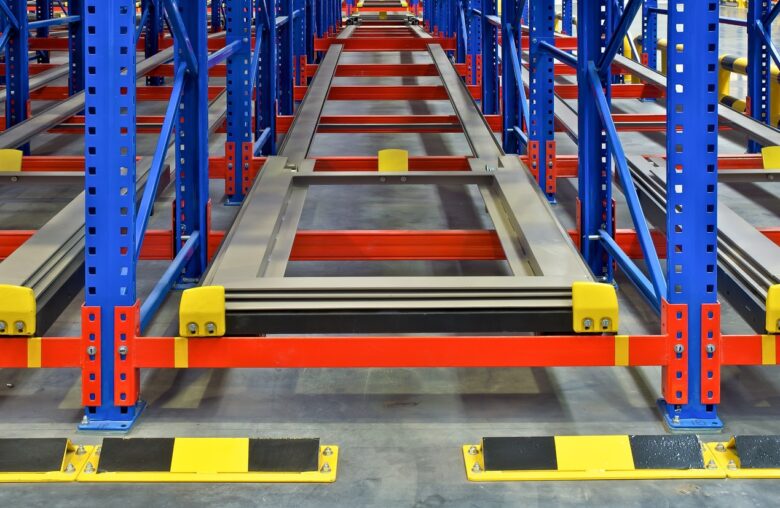
Source: storagesolutionsinc.com
By embracing the power of push back racking dimensions, you have the opportunity to completely revolutionize your warehouse storage system. Push back racking is a dynamic storage solution that maximizes space utilization, enhances efficiency, and streamlines operations. It allows for high-density storage by utilizing depth instead of width, enabling you to store multiple pallets deep within each lane. The dimensions of push back racking are designed to optimize your storage capacity. With adjustable lane widths and heights, you can customize the system to perfectly fit your inventory requirements. This flexibility ensures that you make the most out of every inch in your warehouse.
Furthermore, push back racking offers a gravity flow design, allowing for increased productivity and ease of access. By utilizing inclined rails and carts with brakes, it enables operators to effortlessly load and unload products with minimal effort. Another benefit of push back racking dimensions is their ability to support various product types and weights. Whether you deal with heavy-duty items or fragile goods, this system can accommodate a wide range of loads while maintaining stability and safety. Implementing push back racking into your warehouse not only optimizes space but also improves inventory management. The Last-In-First-Out (LIFO) system ensures proper stock rotation, reducing the risk of product obsolescence or spoilage. In conclusion, by embracing push back racking dimensions in your warehouse storage system, you are taking advantage of an innovative solution that maximizes space utilization while enhancing efficiency and productivity. This revolutionized approach will help streamline your operations and ultimately improve your bottom line.