Creating high-end goods is extremely important not only for customer satisfaction and a company’s reputation, but also for the prevention of recalls, cutting down on unnecessary losses, and for avoiding additional expenses. Thanks to technological advancements and innovation, there are now more ways to implement quality control into one’s facility. Here are some steps to take to enhance your product’s value while maintaining an efficient manufacturing process.
Contents [show]
1. Defining the Standards
Establishing certain production standards that include all requirements, specifications, and characteristics of goods will greatly help with implementing control in your facility. This will ensure that you get superb end-products that meet all the standards. Creating specific guidelines will help employees understand how to properly do their jobs as well.
2. Staff Education and Training
To ensure consistency employees need to receive the right education and training. This will not only enable them to know how to spot any insufficiencies, defects, or abnormalities but can also reduce mistakes, boosting productivity. Having more eyes on the lookout for any possible errors means spotting any problems before it is too late to fix them which would normally result in faulty goods and financial loss.
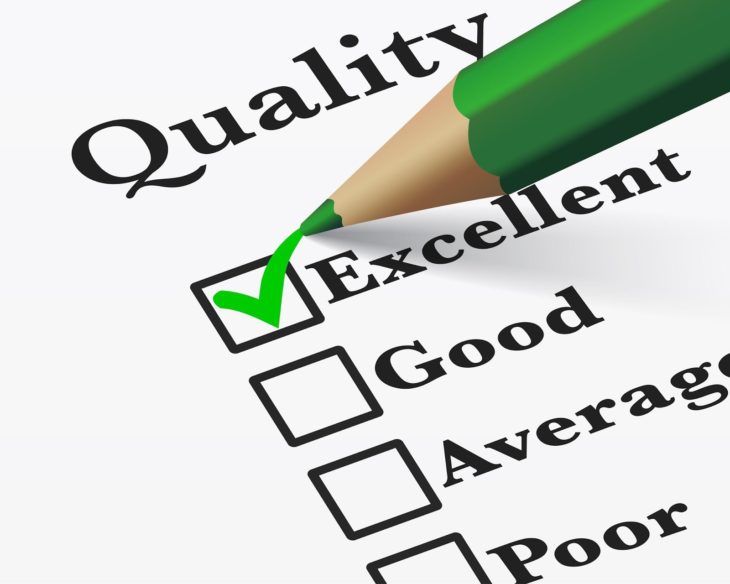
Source: alexgpr
3. Utilizing Technology
There are so many great technologies, automated machinery, and software that can help enhance your manufacturing process, so do not overlook their importance or ignore the benefits they have to offer. Data gathering and analysis can help you boost operations and increase efficiency.
Vision inspection systems can complete several different tasks for you such as to monitor your products via cameras, video, and lighting to ensure they are in the right place, shape, and that your parts have no defects. Certain vision systems can offer assistance to robots, while others can be used for measuring and sorting parts. When integrated into your line they provide a continuous flow of information and can be used for quality control, automated inspections, and much more. You can visit topvision.net to learn more about this technology.
4. Upgrading Equipment and Processes
Upgrading does not mean buying the latest equipment or using the newest technology. There is no need to get rid of machinery that still performs extremely well, although you should consider replacing ones that are very old, especially if they produce large quantities of faulty goods. Outdated processes might also not be optimal for your business, so consider building proper ones that will meet all your production standards. As difficult and time-consuming as this sounds, it will greatly reduce errors, increase speed and quality, and prevent any unnecessary expenses.
5. Regular Maintenance
There is nothing worse for a business than when a production process gets slowed down or completely stopped due to machines breaking down. This is why performing scheduled maintenance is crucial for smooth operation at all times. Regularly performing preventive maintenance will ensure that you do not experience any work stoppage or unexpected downtime.
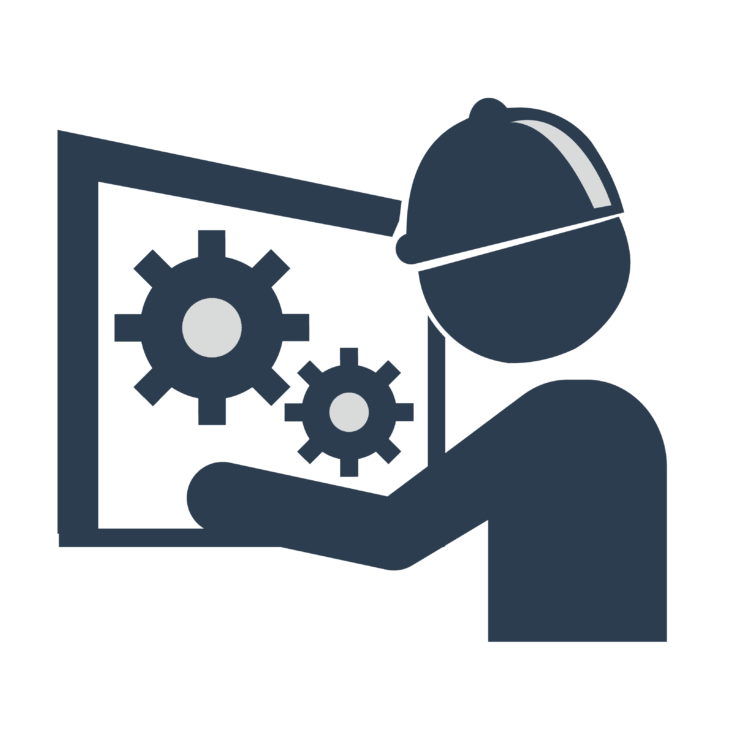
Source: sensrtrx
Conclusion
Making just a few changes to your production process can drastically boost your product and manufacturing quality. No matter how good you think it is, be realistic and accept that there is always room for improvement, regardless of how small it is. This will also help you increased revenue and garner higher consumer satisfaction and loyalty.