In this age of online music streaming, some artists and fans are trashing the idea of releasing in custom vinyl records. Why make plastic when there’s Spotify?
But pressing and buying vinyl records nowadays shouldn’t make you feel guilty!
You see, there have been many efforts to make the production and elements of these physical albums more sustainable like the LA-based vinyl pressing plant UnifiedManufacturing.com and many others.
How do they do it?
Here are some of their efforts in making vinyl manufacturing gentler to mother nature:
Contents
#1: Use of calcium zinc stabilizers instead of the toxic metal stabilizers
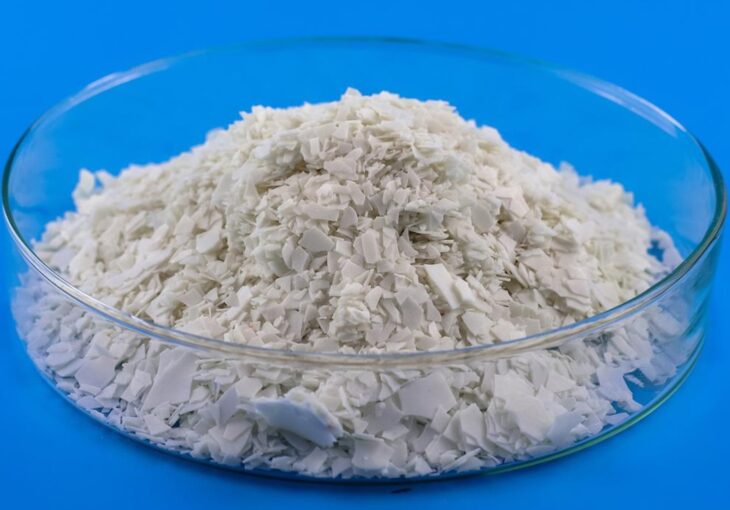
Source: Alibaba
Pressing plants use polyvinyl pellets or grains during vinyl pressing.
These grains or granulates are the initial phase of vinyl records. They are melted and sandwiched by two stampers for 30 seconds to produce the custom vinyl records together with its grooves.
Instead of using the usual additive for such granulates, heavy metal stabilizers, pressing plants turned to producing their custom vinyl records in granulates with calcium zinc stabilizers.
To start, these stabilizers are very crucial additives of plastics as it helps them avoid degrading when heated or melted. So there is no way that heavy metal stabilizers, which are highly toxic, can be removed from vinyl granulates.
To make up for this, they are instead replaced by a more eco-friendly and non-toxic stabilizer, the calcium zinc stabilizer.
#2: Operating using green energy
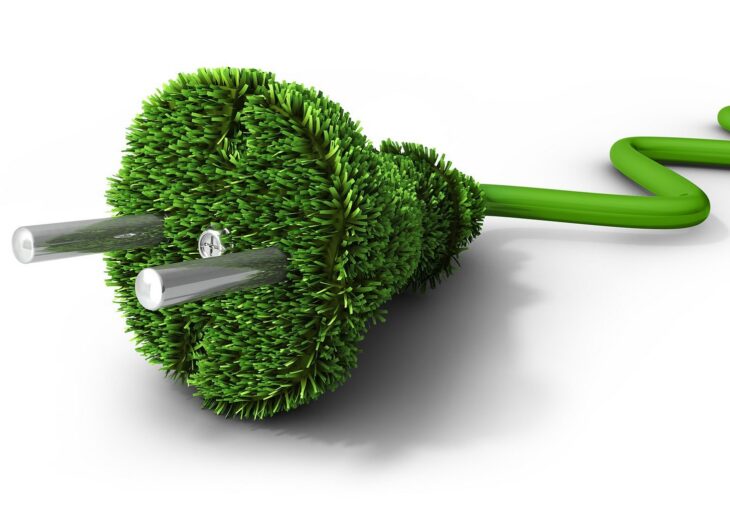
Source: Mitchell EMC
Many businesses from different fields have been trying to operate, manufacture, and produce their products and services with the use of green energy and pressing plants are one of them. Plants and factories producing products need energy to have machines going for the production. Moreover, these plants and factories will also need energy to use for the transportation and shipment of these products.
Since the discovery of natural gases, we have been using them for almost everything we do, which exhausts this non-renewable energy. In addition, this non-renewable energy has pollutant and toxic byproducts. These byproducts affect the health of humans and animals, pollute waters, soils, and the Earth’s atmosphere.
To avoid adding to this environmental problem, pressing plants have discarded these natural gases and replaced them with renewable resources or green energy for their custom vinyl record pressing services. Some of the most used are those solar energies, wind energies, and green gas.
Many of them use solar and wind energy.
Solar energy is from the sun’s energy converted by solar panels while wind energy is from the force of the wind when it turns turbines and converted into energy. Then we have green gas, also known as biomethane, which is a man-made gas from the gasification of biomasses. Biomethane is the purified version of these gases from biomasses through the removal of carbon dioxide from the equation.
#3: Use of FSC-Certified papers

Source: Forest Stewardship Council (FSC)
In the production of packaging and inclusions for custom vinyl records, pressing plants use cardboards and paper. We all know where these papers and cardboards come from trees, and in order to make them, trees need to be logged which is done by some illegally. To avoid buying products made from illegally logged trees, pressing plants have been using FSC-certified products.
FSC stands for Forest Stewardship Council which was established in 1993 to manage forests worldwide. FSC-certified papers and cardboards are those products that have been verified by the FSC to have been genuinely recycled. Unlike those recycled claimed papers, these FSC-certified papers have already been verified, so you will have no qualms if they really are recycled or not.
#4: Soy and vegetable-based inks instead of petroleum-based inks
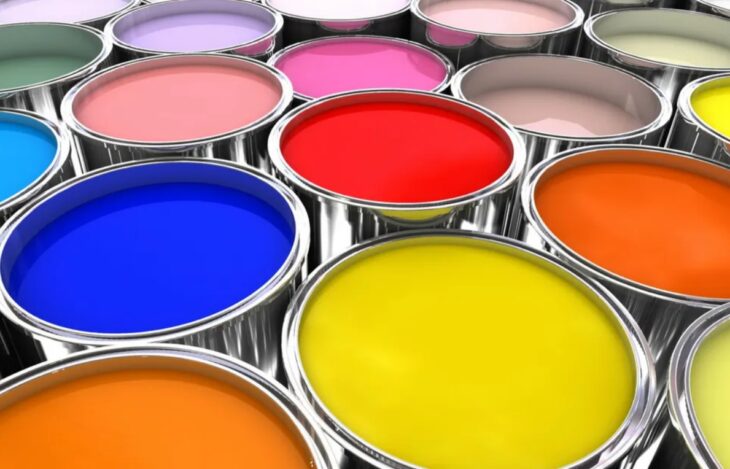
Source: bambooink.com
Another element that pressing plants have replaced to be more eco friendly are the inks used for the prints on the vinyl jackets, inner sleeves, and album inclusions.
Instead of the usual petroleum-based inks that are hard to remove during recycling, vegetable-based inks are used. The most used vegetable-based ink is the soy-based ink which came from soybean plants, and this is due to the inexpensiveness of growing soybeans.
These inks do not only benefit the environment though. Its usage is also a big help to pressing plants because it is inexpensive. Additionally, only a small amount of it is needed for the same amount of printouts that used petroleum-based ones.
#5: Use of biodegradable packaging
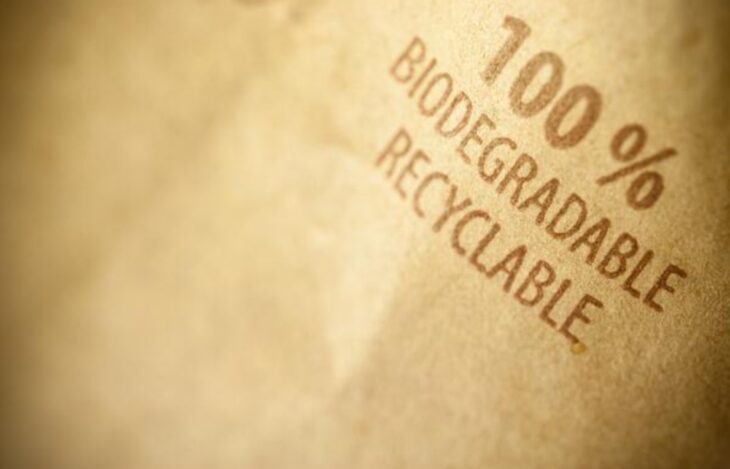
Source: Protega Global
Last on the list is the eco-friendly packaging pressing plants use for the transportation of custom vinyl records.
During vinyl pressings, there surely are parts of the cardboard that become useless and so these things are recycled to be used for the transportation of the vinyl records. Moreover, there are cardboard boxes that become empty that are then used as storage boxes. These boxes are then sealed with the use of biodegradable paper adhesive tapes.
There are many more efforts these pressing plants have made to help clean the environment and I am sure that there will be more to come. So you see, vinyl pressings are safer for the Earth today.
There’s no need to worry about the environment because pressing plants are taking care of that. In fact, streaming music has big environmental impacts that might even surpass the physical format.
Any kind of consumption will have some sort of impact on the environment. We’re here to enjoy life without causing too much harm. Let these efforts made by vinyl pressing plants make vinyl listening guilt-free.