Warehouse inventory managers are liable to be stuck in a rut. This is because optimizing inventory is a constant challenge to meet consumer demand. In order to properly evaluate your processes, as well as your warehouse performance, here are 8 effective tips that will make inventory management run more smoothly.
Contents
1. Track High Sellers
The ability to track orders per client and sales per product is fantastic. There is no better way to position your high-selling products at locations that will make restocking and delivery as easy as cake. Everyone, from the warehouse team to the client and customer, benefits from positioning your in-demand products at strategic locations.
source: ventureglobalsolutions.com2. Identify Key Performance Indicators (KPIs)
Data management and analytic capabilities are the foundations of warehouse management. Without identifying KPIs or define objectives, shipment errors will occur. Costs skyrocket. By identifying which objectives must be met, or establishing a baseline, you will be able to create goals for warehouse and fulfilment that you can measure against to increase the productivity of the warehouse. You can’t have a good day if you don’t know what that day’s mission is.
3. Track Personnel
It’s easy to forget the employees. Therefore, it is paramount to include security protocols for tracking employees. This identification will make it easier to keep a headcount of who is on your floor, as well as who shouldn’t reasonably be there. It will also show you where somebody is in the warehouse, so they can be alerted immediately when it comes time to unload or restock.
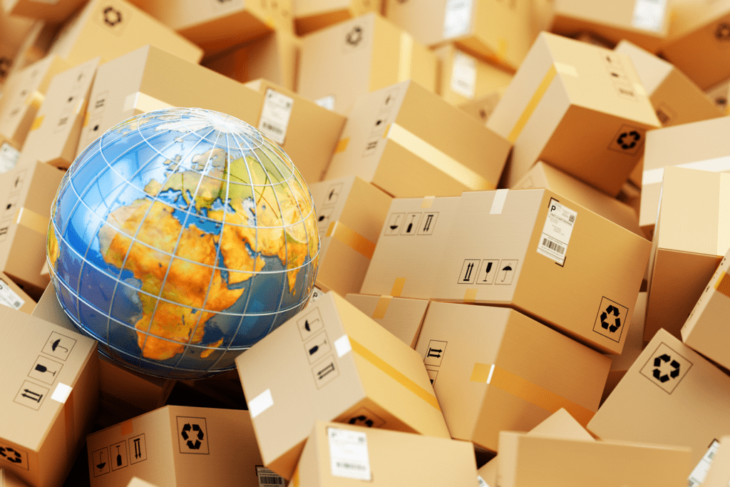
source: blogs.wf.com
4. Go Vertical
Storing products in demand and growth require more amount of space. Have you thought of building up? Products that are stacked on top of each other, making use of the vertical space, maximizes how much cubic footage you have to work with. Less-frequently ordered products can be moved towards the top.
5. Explore Other Options
Do you practice cross-docking? If not, you may be costing your facility time and money. Have you implemented wave picking? If not, complex shipping systems may cause confusion during tracking. Your warehouse management system should allow warehouse-lite options that will put you in the driver’s seat.
6. Use Technology
A warehouse management system (WMS) is a technological tool that allows you to streamline your workflow and increase productivity levels. This is because protocols such as EDI, XML, and HTTP help you implement a database infrastructure, and track the movement of inventory. Your facility will be able to implement more complex and sophisticated logistics.
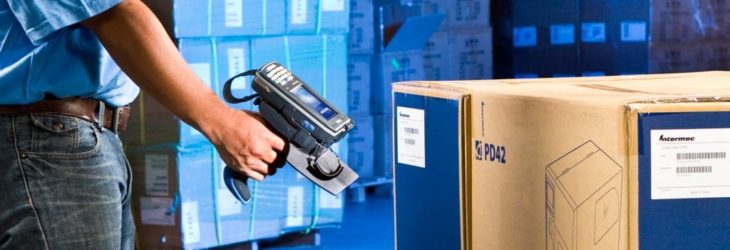
source: itl-keppel.com
7. Safety
The fact is: accidents happen. This puts your business at financial risk, due to litigations and insurance premiums. Therefore, while you’re analyzing your warehouse for increased optimization, put a priority on increasing the safety levels. This means assessing the various risks and designing a way to minimize the hazards. (Employee safety training is a great start.)
8. Re-evaluate Layout
The end of each year (not quarter) is the most optimized time for you to analyse the data of that year. This will show you certain key shifts that will show you how to optimize your layout for the new year. This gives you a time to re-evaluate the demand for products, thus giving you a precious opportunity to maximize the optimization of your facility’s layout.
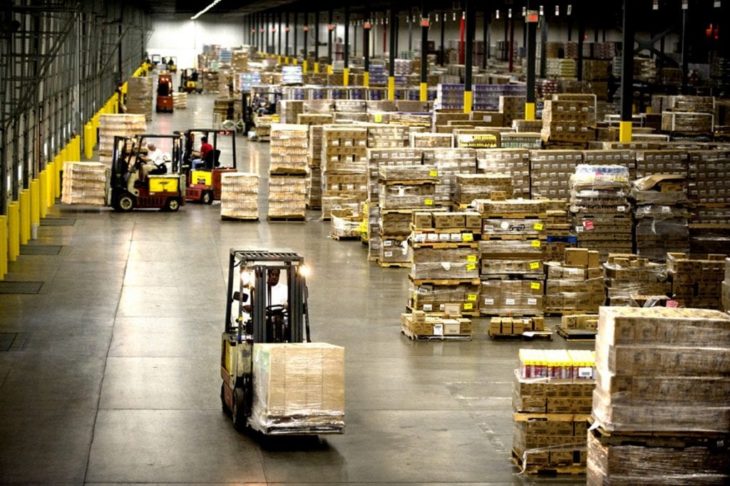
source: medium.com
Conclusion
Proper inventory management can only come from analyzing historical sales and the service level for each SKU. Business functions often determine how inventory levels are managed. With the right critical thinking skills and a willingness to improve things, your warehouse inventory management will be more effective.