The F160 Frace is one of the most striking bikes to be created in recent years. It is produced from a large block of aluminum. The cyclist has to use their legs to move around since it is a manual bike, although it is designed in a way that would make you think it’s electric.
The cutting tools Ceratizit used to create the bike from a large aluminum block make the bike one of the most eye-catching bikes to exist over the years. Below is an overview of some of the important things you need to know about the F160 Frace.
Contents
Features of the F160 Frace
1. Durability is assured through the Dragonskin Coating
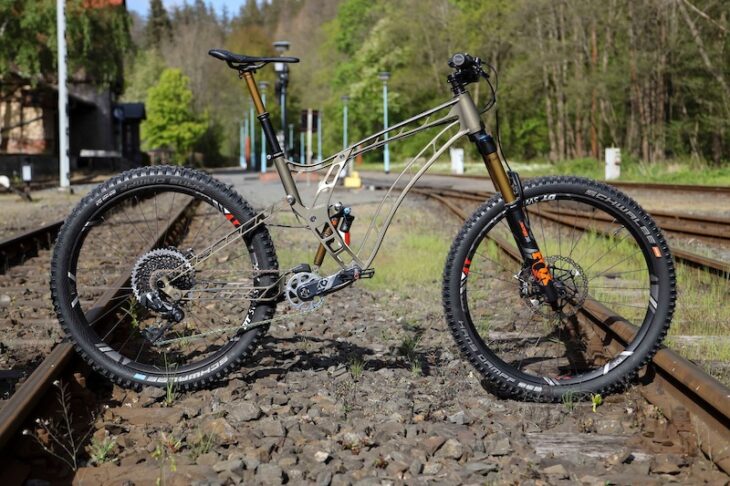
Source: pinterest.com
The bike has a suitable surface coating specifically created for extensive milling. The dragonskin coating well enhances the durability of the milling cutters of the CCR. This feature allows it to withstand the various levels of heat fluctuations.
The dragon skin means the tool is coated in DCL. The chip breakers and the cutting edges are combined, thus providing the milling cutters with the ideal environment to make the bicycle frame effectively machine the pockets.
2. Its Trochoidal Milling Enhances Its Efficiency
A good example is how the frame’s pockets efficiently operate. From a programming perspective, the previous milling process was time-consuming compared to this current machining strategy.
The milling cutter goes to a depth of about 25mm during action then the chips eventually fly. Initially, one could get to their destined cutting depth at a slower pace, but now all they have to do is create a hole and then set themselves ready to leave once they insert the full length of the cutter into the hole.
3. High Level of Speed Is Guaranteed
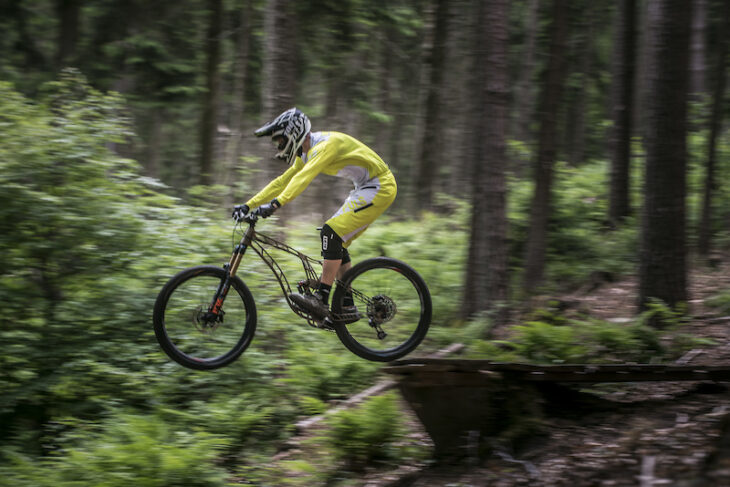
Source: m.pinkbike.com
The CNC professional is viewed in high regard due to the cutting data, which gives it a lasting impression. It is currently running at VC m/min in terms of speed with a diameter of 6mm. In addition to that, it also runs on vf 2000 mm/min regarding its feed speed, making it more intense.
4. Saves the Processing Time by 40 Minutes
Ideally, the bike’s frame structure has numerous pockets that need to be gotten rid of via the milling cutter. The process has nowadays been accelerated compared to how the speed was before. While on the chainstay, one gets to save their machine time by 40 minutes.
Similarly, results are produced when the machining process is changed to the CCR cutter from the seat stay. When in action, this process is completed in 60hours, and the price is high. Potential buyers will have to spend close to 5000 euros. The price is high, but the buyer, in turn, gets something valuable that they might rarely find elsewhere compared to other bikes’ performances.
Professional bikers have confirmed the efficiency of the F160 after testing it out and comparing it with the other bikes. Additionally, the quality of the bike has also been proven through the test carried out by EFBE, which Frace eventually received.
Produced From Aluminum
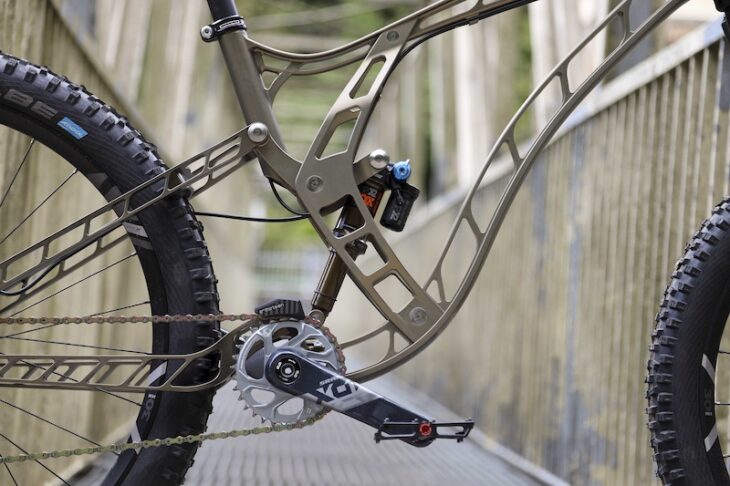
Source: m.pinkbike.com
The F160 mountain bike is an enduring one produced from a large block of aluminum that weighs 70kg. This aspect makes it strong enough to survive the uncompromising downhill with suspension travel of 16omm, inch wheels of 27.5, and a four-link rear suspension. It has zero welded seams, and incorporating the 7075 aluminum highly enhances the production.
The journey of Creating the F160
A former machine operator first created the F160 Frace at CNC Bernd lwanow. After creating the bike, Bernd tested it on two professional riders since he is not one himself. The feedback received was positive, thus leading to the production of more versions of the F160. The project took two years to come up with the end product fully.
Any engineer cannot randomly wake up and choose to work with materials like the 7075 aluminum. This aspect only shows that Bernd lwanow was confident in his craft and knew what he wanted to achieve. He had always wanted to create his bike before he eventually ventured into the automotive industry to create individual parts.
Bernd didn’t want to create just anything; he wanted to come up with something unique. Lucky enough, his company had favorable conditions to enhance the production process of the bike to be completely milled.
He started by designing the design in CAD before executing the production process of the final product. With the help of Frederick Tobiasch, his test pilot, he came up with different versions till they settled on the current one.
The idea came about carrying out web research he finally came up with the perfect design idea. Currently, no manufacturer in the market has been able to create a similar mountain bike that can match up to the F160 bike standard. This factor has made Bernd eager and more passionate about matters to do with milling cutters.
The production process begins with a large block of aluminum which is usually stiff and very tricky to weld. Different segments are produced from the slab and then joined by titanium screws.
Once the frame is produced, it is eventually tested by the Germany assessment group that assesses bikes, and it is aesthetically pleasing. The bike comes in 2 wands in cells 27.5 inches apart and weighs 16.3kg. Even though it is not the highest bike globally, it is the coolest.
What is the Retail Price of The Bike?
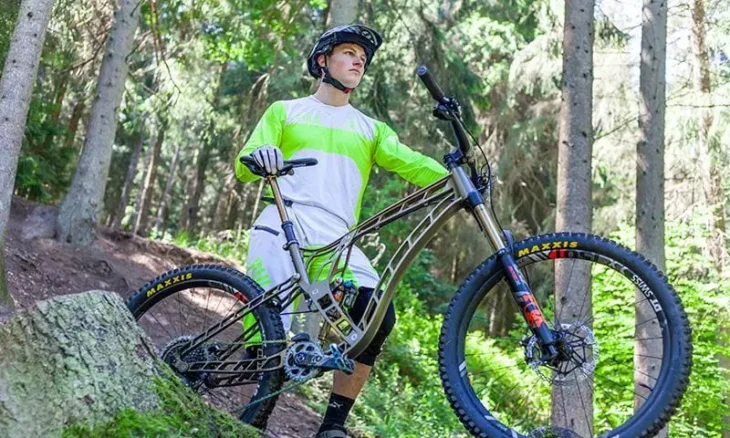
Source: coolsten.de
Lwanol hopes to produce 50 frames annually, and each one of them is set to retail at about 5.62 dollars. Complete bicycles are set to cost about 8.419 and 13.472 dollars, depending on the components.
Conclusion
There is only one-way cyclists can stand out from the crowd, especially if they are those types that appreciate bikes with appealing aesthetics and not just for their durability and performance, through the Frace F160. We hope that the above information has given you a clear description of this new masterpiece. All the best in your next cycling escapades, guys!