So, what is Bursting Strength of Textiles?
Simply explained, a textile’s bursting strength is its potential to resist breaking under pressure exerted on it. It’s a textile’s property to oppose stress and tension spread from all directions.
Contents
Do Ordinary Commodities Require to Undergo the Bursting Strength Test?
The answer is, yes. Ordinary commodities, for example, trampolines, covers for trailers, compactor enclosures, swimming pool covers, tarps, agricultural baggers, among others, must undergo the test to determine their bursting strength. That is because they are materials that must withstand weights.
The test will make sure these fabrics meet their necessary expected standards.
The Commonly Applied Criteria for Fabric Bursting Test
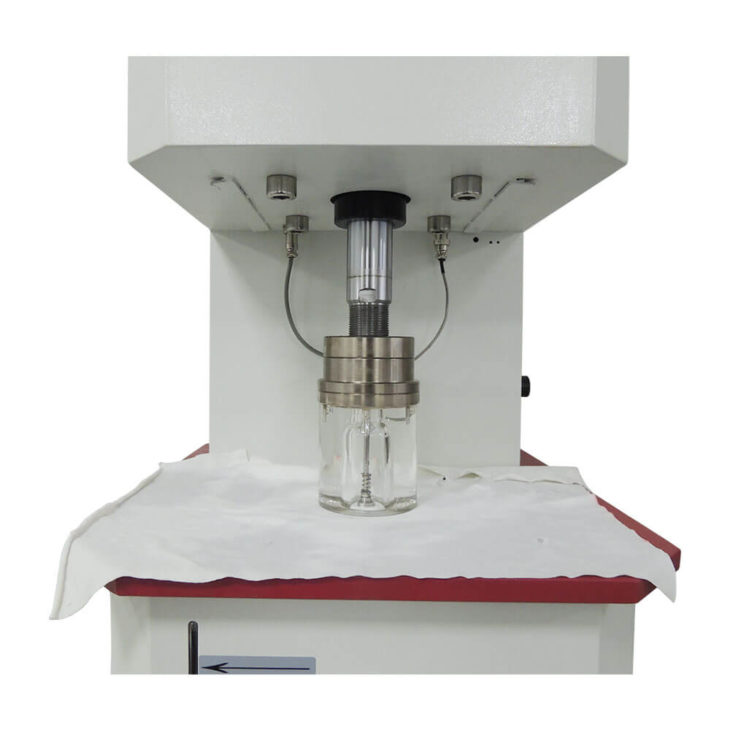
Source: testextextile
Typically, to determine a particular material’s bursting potential, there are three main methods used; the steel ball method, the bursting criteria, and the marble bursting technique. They are all used to determine the bursting strengths of textiles, but their application varies with the textile industry.
Countries like Japan, Australia, the United States, South Korea, Canada, among others, majorly use the Hydraulic Burst Test.
However, in China, concerning the ISO 13938-1* (GB / T 7742.1 “Burst Performance of Textile Fabrics-Part 1: Determination of Burst Strength and Burst Expansion Hydraulic Pressure Method”) a modified testing criterion has been initiated.
*ISO 13938-1 & ISO 13938-2: 13938-1 Hydraulic pressure source, ISO 13938-2 Pneumatic pressure. Based on findings from ISO, there isn’t any remarkable contrast in the bursting potential results reached using the pneumatic or hydraulic burst tests for loads not exceeding 800 kPa. This pressure extent extends to most of the performance degrees required of overall fabrics. For unique apparel needing high point bursting stresses, the hydraulic burst test is more favorable.
Test principle
The relevant sample is braced upon a stretchable diaphragm then the liquid force is applied below the diaphragm. The hydraulic volume is added progressively at a regulated speed and noted. The process continues up to the extensible membrane, and the specimen is enlarged to limit where the specimen bursts. Afterward, it is recorded as the calculation of its burst strengthens.
The marble burst criterion was used before the correction of the national quality “cotton knitted underwear”. Simply, a round marble measuring 25mm was applied in testing the knitted material. The test criteria recorded In the GB / T 19976-2005 (Determination of The Bursting Strength of Textiles) levels enacted in 2005 has two variations contrasted to the preceding one. To begin with, the breadth of the steel ball/marble is 38mm. Secondly, what determines the force testing instrument is a globally applied Constant Velocity Elongation strength meter.
Bursting mechanism
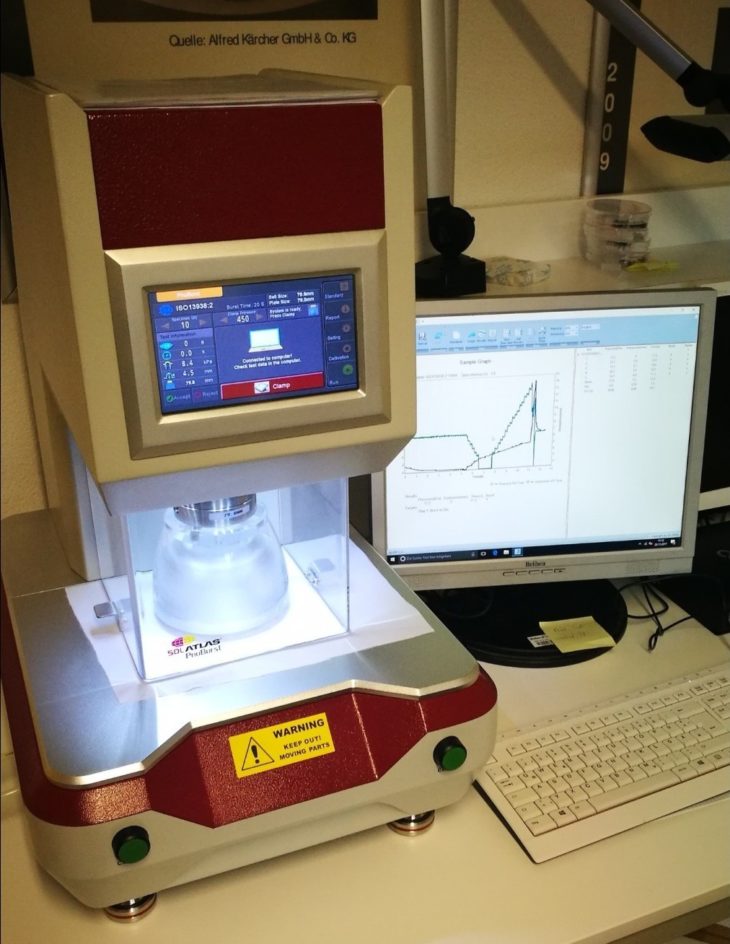
Source: weber-leucht
The plain weave will develop a tear parallel to the lengthwise direction of the textile, causing more bends to form across the course of the fabric. The coil is then disconnected.
Three methods have similar failure mechanisms
Weak Loop Theory
-
Woven material
The distortion of the content in the weft and non-warp directions is brought upon by the two sets of weft and warp threads breaking off each other. The lengthening and distortion are stronger than the weft and warp directions. Under the tension of the upper force in the direction and toughness with minimal contortion, the most vulnerable section of the thread breaks and then shears parallel to each other in the weft or warp directions. Therefore, the cut is even.
In case the warp and weft distortion capacities of the material are the same, the weft and warp threads shear simultaneously during bursting. The resulting split is typically T or L-shaped, stipulating that the weft and warp fabrics undertake the most crucial role concurrently.
-
Knitted Material
The coils are twisted into a single piece, and then they are stretched and distorted until the material breaks.
-
Non-Woven Material
Basically, it’s the shearing of fibers and the slacking of the fiber connection. The upper aperture is a protruding baggy fiber bag, and the breaking is the slacking of the fiber web.
In case the knotted fabric is put under tearing force, it will result in destroying the most delicate point first and then initiate a tension deposited at this distortion point. As the test progresses, the plain weave material is destroyed. That will cause an increased number of spread loops on the plane direction. Also, the cuts will keep on expanding towards the longitudinal side. The pearl material will shear more threads, and the cuts will widen around the edges.
Test Results
The findings of the various test criteria are contrasted as follows:
- The breadth of the marble ball is smaller than that of the steel ball, and the bursting strength acquired by the marble ball is also lesser than that of the steel ball.
- The three different test procedures have the same failure techniques, and the form of the splits after the material is destroyed are typically similar.
- The findings of the three different test criteria have a better direct connection with one another. Therefore, there is an excellent association between them.
Test significance
The tension power is less fit for assessing materials like knitted and lace fabrics when their bursting strength is involved. Then the material is destroyed; it’s usually put under pressure in the weft, warp, and diagonal directions. That is mostly applied to elements like the weft-knitted textiles, which possess the traits of lateral shrinking and vertical expansion.
In case the tension strength is applied, the weft, warp, and diagonal directions shouldn’t be tested at the same time. Also, the bursting potential can be assessed once for the strength potential of the material.
Testing procedure
For more information regarding the bursting strength test, kindly click here.
Equipment calibration
- It’s essential to confirm that the equipment is up to the required standards and that its parts are functioning correctly.
- If required, standard films such as an aluminum foil can be applied to substantiate the inclusive execution of the bursting strength tester.
- The stretchable diaphragm should be changed in case it’s destroyed. Before clamping the specimen, make sure to stretch the membrane to a particular limit and study its shape. If there’s a noticeable contrast from the regular spherical-crown appearance, then change the diaphragm.
- To clamp the specimen, first, cover the example on the diaphragm while on a level and stretch-free state and secure the sample with a ring clamp.
- Then, ensure that the specimen isn’t destroyed by the installation when clamping.
- Before commencing the testing process, ensure to try-out the new prepared specimen in advance following the required regulations. Then sturdy if the bursting strength of the material up to tearing is finished within the set time frame. If otherwise, the pressure range should be modified while referring to the standards of the equipment. That ensures the average bursting time appears within the stated span. The overall time for fabrics is stated as 30 ± 10s, while the wool material is 15 ± 10s.
- For the deciding experiment, apply the modified force rate to test the specimens one by one and compute both their bursting expansion and strength. In case the sample bursts at the boundary of the ring of the installation, another one should be used, and the test repeated.
- For the diaphragm correction number, apply the same hydraulic speed as the above experiment. Before clamping the specimen, attach the diaphragm with a clamp and extend it until the force needed for the average extension and expansion of the sample.
Test Result Valuation
- Calibrate the bursting potential of every specimen, which is the aggregate force of the burst minus the power needed to destroy the film.
- Compute the bursting strength of every specimen and the average bursting potential of al the samples.
- Remember to detail the type of equipment applied for the experiment.