Plastic injection molding, in addition to making certain tools necessary for this procedure, is a service thanks to which we can complete the entire process of plastic parts creation. We could say that it’s the most commonly used method in today’s processing of this specific material and units produced by this type of treatment can come with various levels of complexity and surface quality. Thanks to this system, which mostly uses thermoplastics for this purpose, we can use such objects in our households or workplaces. Whatsoever, some of them are present on a daily basis all around us.
This procedure essentially consists of heating the plastic mass in a special cylinder and injecting it under strong pressure, making the material reach a relatively cold pattern through a nozzle. This has reached a high degree of perfection both in machines that are now almost automated, and in tools that enable high productivity with their solutions. Services in this sphere are pretty on point and in case you click here, you can even see how the injection moulding process looks and get better informed about the conditions, which might be pretty helpful if you don’t know much about it.
So, today maybe you’d want to check out seven main parts of this method – just to make sure you understand what the necessary steps look like. And, of course, get to know how those countless plastic objects that we use in our kitchens, workshops, garages and bathrooms are actually made.
Contents
1. Making a concept of the product
Before the real molding occurs, we must first know what we’re actually doing. If we do it for ourselves, the first step involves designing the shape and size, defining the purpose and the rest of characteristics that the object we want to create should have.
When we work for the client, it’s quite significant that, respecting their wishes, we create a concept in cooperation with them that will agree with what they have imagined. Anyone who knows at least something about this will agree that this is, logically, actually a crucial thing without which we wouldn’t know what exactly we’ll do with either if we have the machine or the material. Creativity is another unavoidable item here, just like practicality, in order to get the final product that satisfies the necessary characteristics, application and has all the necessary parts.
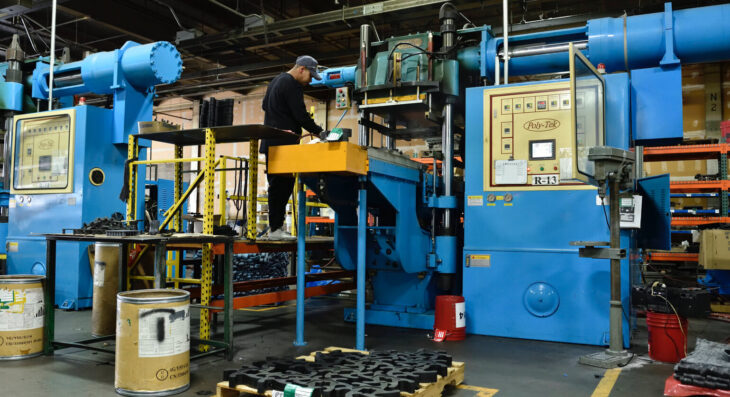
Source: poly
2. Mold design
Once we have determined what we actually need and what we want to make, it’s time to create the appropriate pattern shape for the desired product. They’re usually made of metals such as steel (a harder and softer variant), which is one of the more expensive materials to make, aluminum and some types of copper.
Why is this important? Logically, because the precision of the shape of the product that we’ll get after putting the mass in depends on the shape in which the pattern is designed. Every mistake in the steps here can be reflected in the final outcome, so it’s required to pay a lot of attention to this part. Failure to do so will result in defects such as a poorly designed draft or gate that’s out of place or of the wrong size.
3. Mold closing
When the pattern and the idea are ready, we’re leveling up to the next step – mold closing. The pattern usually consists of two parts, that is, two equal halves that need to be joined to obtain a complete unit. Experts use a special type of clamp for this, which needs to have solid strength in order to perform this in the right way.
It should be borne in mind that the process of opening and then closing the unit can take some time, depending on the size or complexity, but once that happens, the machine is ready for the main part – which is plastic injection.
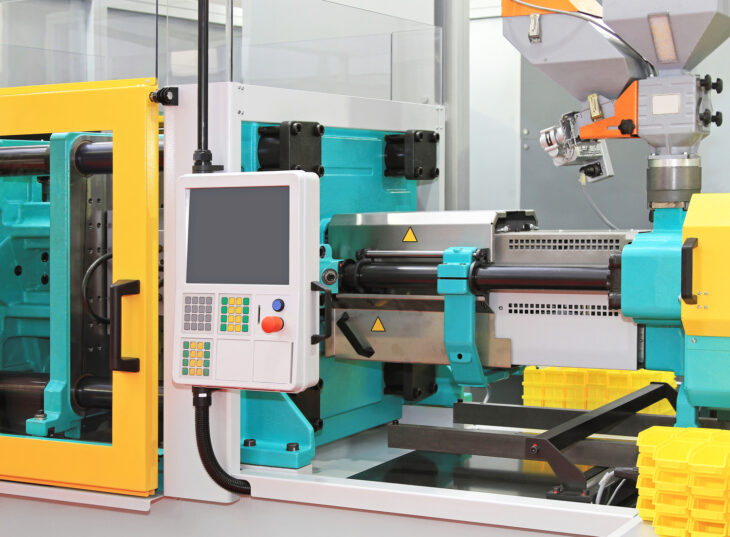
Source: processvalidation
4. Injection process
As we mentioned in the introduction, a key part of the process is happening right now. The next operation is to inject the melted plastic into the pattern cavity. At that point, the injection element, in this case the screw, acts as a piston. Upon completion of the filling of the cavity, there comes switching to a subsequent pressure in the cylinder.
The subsequent pressure is generally lower than the injection pressure, as there’s no longer a high resistance to the flow of the melt. Its task is to direct the additional filling of the mold cavity. The quantity of material that gets inserted into the mold in one go is called a shot and can be considered a kind of measurement unit when it comes to this procedure. This part can take a little more time, depending on the size of the object being built, but also the strength of the injection unit and some other factors.
5. Cooling
It’s significant to note that the cooling process itself begins as soon as the plastic comes into physical contact with the mold. As is the case with any similar substance that is soluble, this means that the mass will shrink inside in the desired shape without any problems, creating exactly what we wanted. But of course, for that to remain the case, we must give the masses a chance to cool completely.
Sometimes there might be problems if the filling fails to be done properly, and bumps, holes and other damage can occur, but the good news is that it can all be fixed while everything is still ‘fresh’. Another crucial factor is the above-mentioned respect for the predetermined deadline for consolidation. If it’s a thicker layer of plastic or a special type that we use, it can vary, ie. take more time.
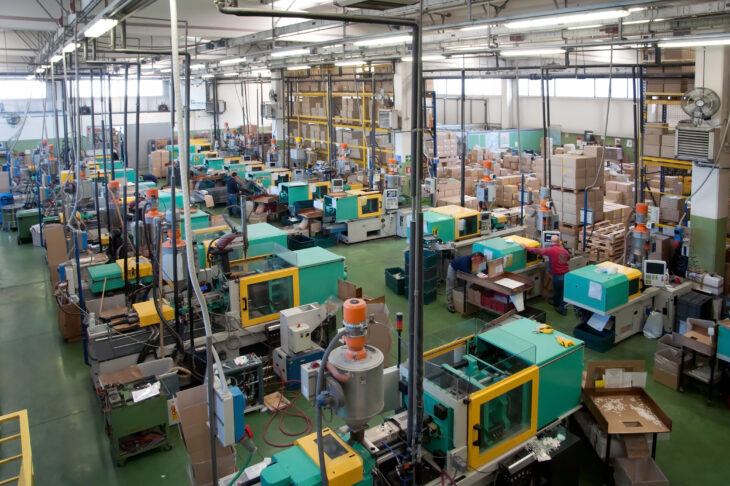
Source: themanufacturer
6. Ejection
After the required time has elapsed for the mass to cool, the mold is opened by the same technique that was used to close it, in order to squeeze the product out of it. With the help of a special mechanism that includes ejector rods and specific ejector pins and their moving, the object is removed from the mold.
Those who work on the machine usually reserve a special space under it in which the object will fall when it’s out. After that, excess pieces of plastic are removed from the product, as well as bulging parts or any deformities in case we missed them during the process.
Injection molding is one of the most widespread technological procedures for treating plastic materials. The development of new materials and the increasing demands in the exploitation of products obtained by it have conditioned the development and improvement of various molding procedures. For this reason, innovations and new methods are yet to be expected. This will certainly result from this sphere and enable even more advanced processes – and we can’t wait for these times to come!