In any business, things break, wear out, and get repaired or replaced. Itโs a cost of doing business and part of operations. For facility and operations managers, the way those fixes are made can make or break their job and workdays, and thatโs where work order management comes in.
Work order management systems consolidate and manage reactive work orders, preventive maintenance work orders, and asset tracking and management. When it comes to asset maintenance, the adage โpay now or pay laterโ has tremendous relevance.
Contents [show]
Preventive Maintenance vs. Reactive Maintenance
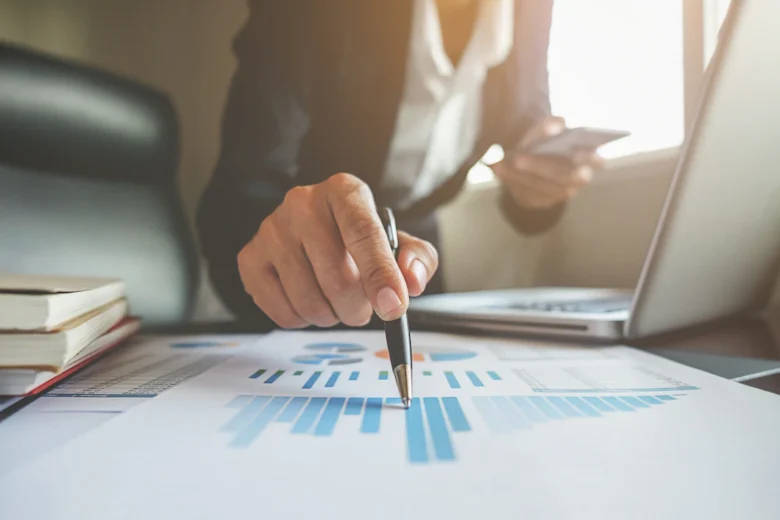
Source: freepik.com
Reactive maintenance is corrective and performed after equipment breaks down or fails. Many consider it a stop-gap measure since it doesnโt tackle the problem at its root. Since reactive maintenance often requires emergency repairs or replacements, it can be expensive. Add to that the cost of unexpected downtime and you get a clear picture of its cons.
Preventive maintenance is a proactive approach to protecting equipment and systems, with scheduled service performed on equipment, facilities, systems, and other assets based on real-time data insights to prevent problems from occurring. A good preventive program can help extend the lifespan of equipment or a facility and improve its overall performance. Think of it like an oil change or tire rotation for your car.
With improved equipment reliability, preventive maintenance can also reduce the need for repairs and their associated costs. A well-designed schedule will increase uptime and reduce the cost of ownership to enhance the health of your business.
To be effective, preventive maintenance requires planning and preparation, and one of the most important tools is a schedule to outline when each task should be performed and who is responsible. Following a schedule ensures regular inspection and maintenance that prevents small problems from becoming major issues. A schedule can help identify trends in operations and performance for go-forward planning.
Creating a Preventive Maintenance Schedule
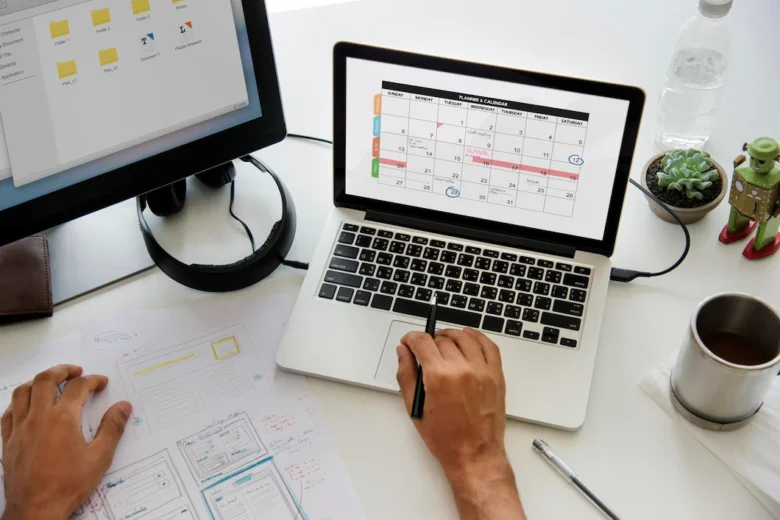
Source: freepik.com
Keep some points in mind as you plan and implement a preventive maintenance schedule:
โข Conduct inspections regularly at planned intervalsโmonthly, quarterly, annually. The timeframe depends on your business needs and the kind of assets you have in place.
โข Assign trained and certified personnel to complete inspections.
โข Include all equipmentโ regardless of age or condition and including new or never-used assetsโon your schedule.
โข Document every step in the maintenance task sequence, no matter how small it seems.
โข Review and update your schedule regularly, especially after changes in your equipment or operations.
Automating Preventive Maintenance
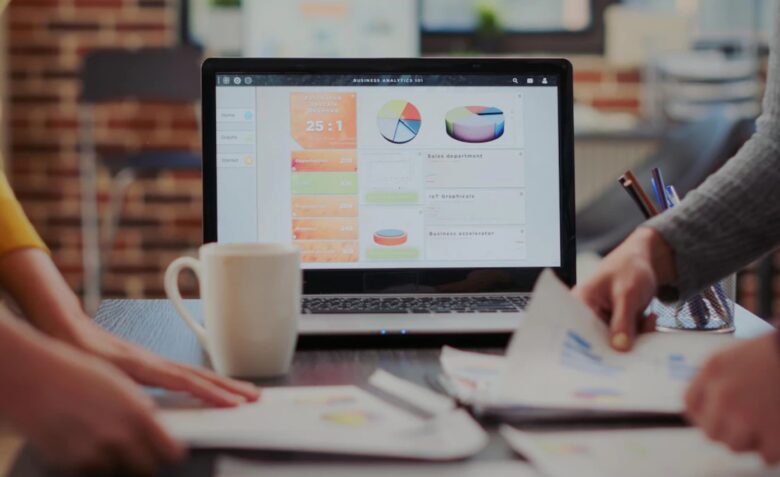
Source: freepik.com
To assign timeframes to a maintenance schedule, engineers use predictive analytics, machine learning, operational data, and asset health monitoring to forecast servicing needs and minimize operational risks across facilities and organizations.
A good schedule drives preventive planning and budgeting. A great schedule relies on powerful technologies to automate the process.
โข CMMS: One of the best tools to create a preventive schedule is a computerized maintenance management system (CMMS), which looks at data points such as equipment age and usage, past maintenance history, and operator input. CMMS enterprise-level solutions are typically used by large organizations, but smaller businesses can benefit from them just as well. Software includes work order management, asset tracking, and preventive maintenance scheduling that can be customized to fit your organizationโs needs. Every function can be accessed, viewed, and updated from a smartphone or tablet.
โข CMMS preventive maintenance software automatically generates and directs work orders to the appropriate technicians. Once a work order is complete, the technician updates and logs it in the system for reference. If a planned inspection reveals faster or greater wear than expected, the software can schedule a replacement before the part fails and causes downtime.
โข EAM: Enterprise Asset Management (EAM) is a type of CMMS software designed specifically for managing equipment assets. Benefits include its ability to support optimization of asset lifecycles and integrate with other business systems, such as accounting and Enterprise Resource Planning (ERP) software.
โข ERP: Enterprise Resource Planning systems connect maintenance planning, work order management, supply chain insights, and asset tracking, ERP software to help improve communication and collaboration. Additional modules include HR and customer relationship management (CRM).
Types of Preventive Maintenance
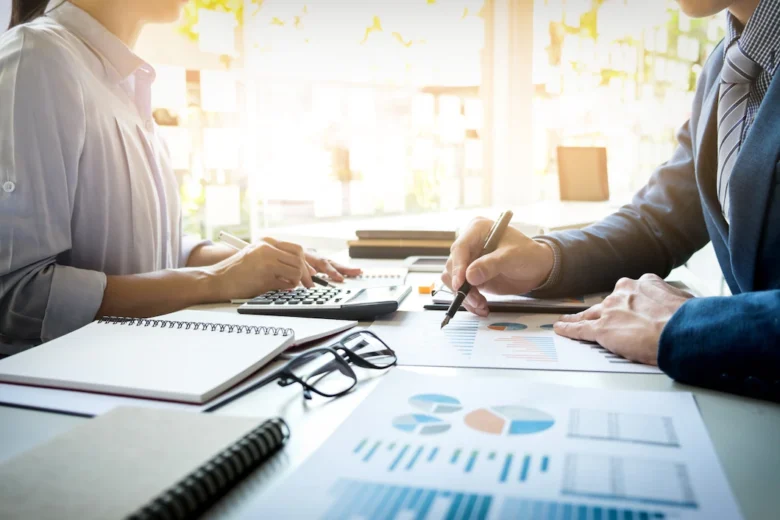
Source: freepik.com
There are six key categories of preventive maintenance, but two have powerful benefits and impact:
โข Predictive Maintenance: Predictive maintenance uses data to predict when an asset will need to be serviced, create usage-based maintenance forecasts, and even determine when an asset is due for replacement. Itโs generally very accurate and guided by preventive maintenance software and is typically used for mechanical and electrical assets such as motors, generators, pumps, and compressors.
Organizations can also use predictive maintenance to identify trends in asset performance and subsequently adjust the way in which it is operated or maintained for improved performance and lifespan.
โข Prescriptive Maintenance: Although similar to predictive maintenance, prescriptive maintenance takes asset data usage to the next level. Through machine learning, predictive analytics, and AI, prescriptive maintenance not only predicts when an asset requires servicing; it prescribes the best way to do so.
Prescriptive maintenance is still a growing industry, so its cost can be prohibitive for some organizations. Typically, itโs reserved for the most critical assets such as production machinery, power generation equipment, or state-of-the-art microscopes in a campus-based research lab.
The ROI, however, comes through reduced downtime and improved performance, which makes it worth considering when critical systems are in place and thereโs investment potential in an operating budget.
The Preventive Maintenance Workflow
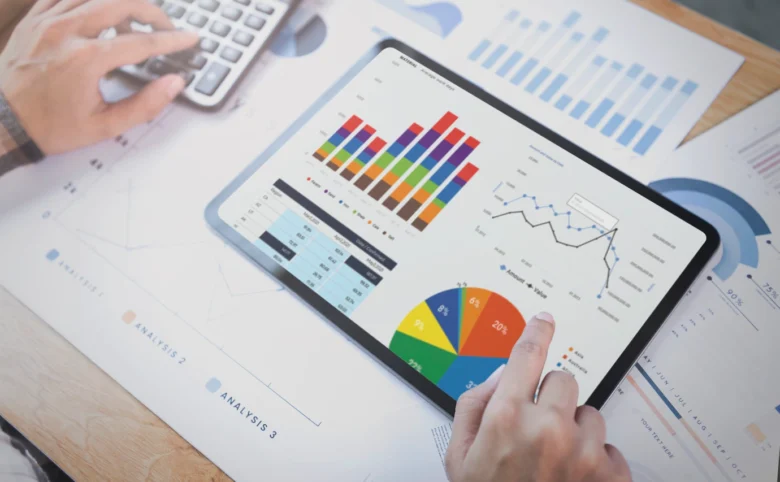
Source: freepik.com
The key to creating an effective preventive maintenance workflow is finding the right balance for your organization to avoid over-servicing your assets or being caught unaware when an issue comes up. Consider these steps:
โข Define and assess the criticality of your assets. Not all assets are created equal. Some are more critical to workflow continuityโsuch as production machinery versus an office printer. Once youโve identified your most critical assets, you can determine their need to be part of a preventive maintenance plan and begin to plan the frequency of their service. Assets that are subject to wear and tearโor whose failure would significantly impair operations, like HVAC systems in a school districtโmight require more frequent servicing.
โข Collect data on your assets. Data can be used to help you make many decisions about preventive maintenance and can be collected in multiple waysโthrough manual tracking, with sensors (i.e., vibration detectors), or using maintenance software. Software tracks an assetโs service dates and predicts when it will need servicing again.
โข Organize your resources. Once your data is in place, organize your resources, such as tools, replacement parts, and trained staff. Consider how a task will be completed, who will do it, its associated risks and costs, and other factors that impact operations.
โข Build a strategy. Consider regulatory requirements, management of multiple preventive tasks, and how youโll deploy your resources, such as creating a work order for every preventive task. In such a case, scheduling them in maintenance software will keep you on track.
Preventive maintenance is just one component of work order management but can reap generous rewards for any organization, especially when facilities, equipment, and systems are physically distributed like a college campus or school district. Learn more about work order management systems at https://www.facilitron.com/facility-owners/work-order-management/.