Have you ever thought about how goods are produced in a wide range of industries? Household components, automotive components, bottles and even toys – it is all created as a product of injection moulding. How much effort it takes to get it all done and what the whole process looks like – find out below.
Contents
What Exactly Is Injection Moulding?
This is a technical procedure of forming shapes by using moulds. Things like plastic, synthetic resins, etc. are being heated at a certain temperature level, liquefied and transferred to special moulds. Afterwards, must cool down in moulds in order to form a contour that you desired. Since this procedure requires using a special syringe, it resembles injecting fluids. Therefore, we call it injection moulding.
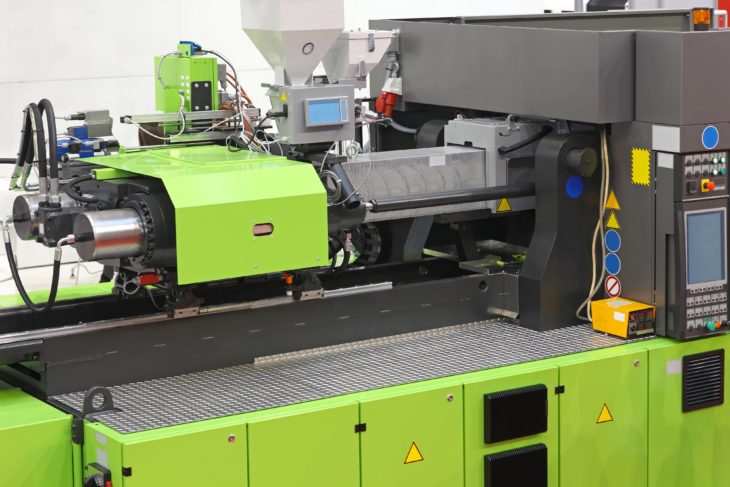
Source: creativemechanisms
How Does It Work?
This procedure must follow a few specific steps. First, the structure is heated to a specific temperature level. It is liquefied and transfused into the moulds, where it stays until hardening. After that, the finished products are ready to be taken out. Thanks to injection moulding technology, different parts or shapes, can be produced very fast and continuous, as well in large quantities. Many companies are specialized in design, development and manufacturing of a wide range of moulding products and services. According to jasonmolding.com product customization, fast production speed and reducing assembly time are some of the greatest benefits of injection moulding. Therefore, this technology is mostly used for making products in many different industries.
Injection Molding Machinery
There are many different types of machines used for injection moulding. Some of them are run by servo motors. Others are hydraulic or hybrid machines, run by combining servo and hydraulic motor power. Though they may be driven by a different power, these machines have a typical structure. They all have the “injection component” which directs melt-down matters into the matrix. There is also a clamping part which runs the mould. In recent times, people in this industry adopted using CNC technology in using the injection moulding machines. That fact brought to the major popularity of machines that can produce swift injections with programmed management. Then again, several specialized machine types are also being used. Some of these models can form the light guidance plates that are used for LCD monitors.
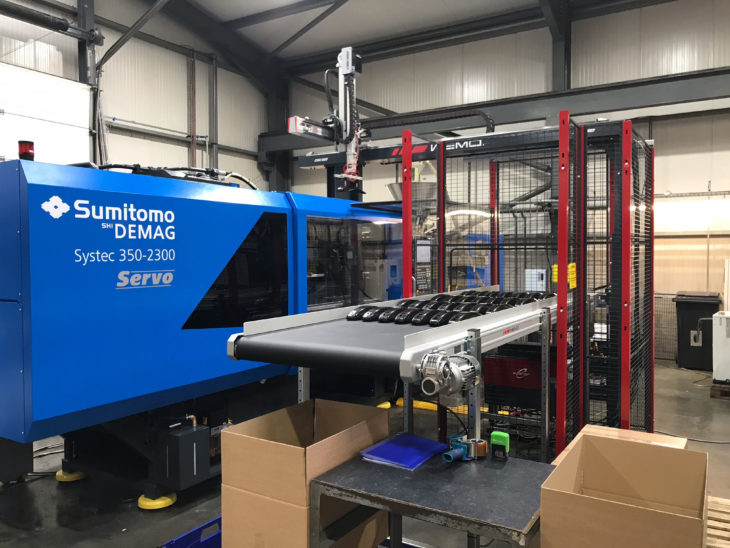
Source: maltonplastics
The injection molding service is a cornerstone of modern manufacturing, enabling the efficient production of complex plastic parts.
This versatile process involves injecting molten plastic into custom molds, creating intricately detailed components with high precision. It’s utilized across industries for creating everything from automotive parts to medical devices. Injection molding offers advantages like rapid production, minimal material wastage, and design flexibility. With the capability to produce large volumes of parts with consistent quality, injection molding services play a vital role in meeting diverse market demands while maintaining cost-effectiveness and product durability.
The IM Process
The whole procedure starts with taking resin-pellets and pouring them into the tank which is the entry station for this material. After that, pellets are exposed to high temperatures up to their melting point. They are now liquified and prepared for injection. Afterward, it is pushed throughout the sprinkler of injection department, previously delivering the melted solution to the other side of a die canal. That element is called “the sprue”. After that, it goes through branched parts into the cavity of the mould. After this substance cools-down and when it solidifies, the mould starts to open, and the moulded element is being squeezed out. For a complete procedure – sprue and runner are being cropped from the element.
In Final
Even though this procedure may seem too complicated, it is quite a common method of manufacturing. It is a very efficient method of producing everyday items like plastic bottles, electronic housings, car components, toys, etc. This procedure is a very cost-effective way to produce both – functional prototypes and parts, as well as final-use products.