The famous Chinese general and military strategist, Sun Tzu, once said “the line between disorder and order lies in logistics”, this comment not only applies to the logistics industry as a whole but also to warehouse management systems. Warehouse mistakes are commonplace, leading to all sorts of unnecessary dramas and even injuries, something operators can and should avoid, at all cost. From poor health and safety procedures, badly designed layouts to the use of outdated management systems, in this article we will explore the top five mistakes found in warehouses and how to improve them.
Contents [show]
Bad Facility Layout
A facility with a badly designed layout can cause more warehouse headaches than anything. Operators need adequate space in a warehouse, ensuring that all areas are easy to access and allow for effortless picking and packing. If operations are difficult to perform in your space, it may be time to consider redesigning allowing work-flows to becomes seamless and time efficient.
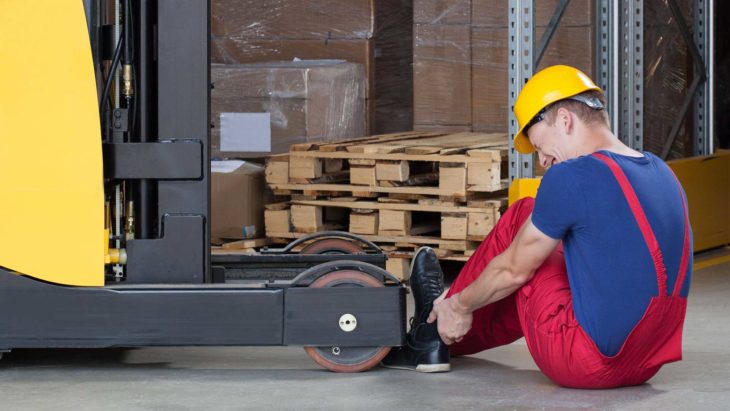
Source: supplychainbeyond
Lack of Safety
Safety in any warehouse must be every operators priority. Without adequate safety procedures in place, people get hurt and lives are unnecessarily risked. According to forklift statistics researched by McCue, “Forklift accidents result in serious injury total 34,900 annually,” in the US alone. If more logistics companies dedicated greater time and energy into Occupational Safety & Health Administration (OH&S) there would be far less accidents and more procedures in place to deal with unsafe situations. Lack of warehouse safety is a mistake too many operators make, leading to tragic situations that could have easily been avoided.
Too much paper
Paper procedures should be a thing of the past, however a large amount of logistics companies still heavily rely on this out-dated mode of operation. As the logistics industry becomes more competitive it’s essential that operators realise the efficiencies and cost savings achieved when moving their systems and procedures from paper to tech. Logistics software company CartonCloud states, “ Whilst there’s some resistance to ‘keep things simple’, paperwork creates other difficulties and delays in productivity. A software solution can maximize productivity, reduce user-errors and avoid ongoing issues with misplaced paperwork.”
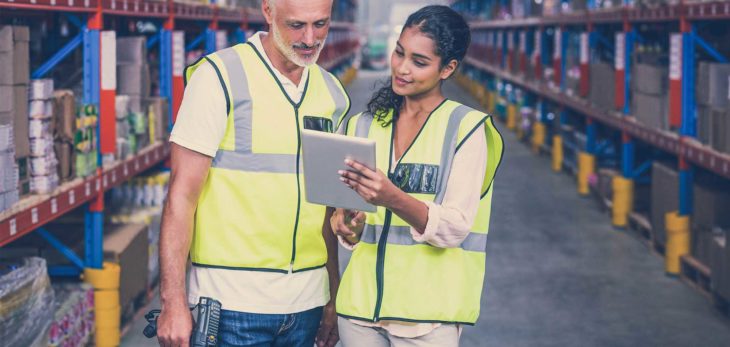
Source: securedgenetworks
Decent signage and shelf labels
Ensuring that all of your inventory is clearly labeled saves time and money. Yes, barcodes work, however, shelves and signage should be ultra-clear and identifiable beyond just a simple barcode. Embracing bright colours, clear aisle markers and large hanging signs, helps workers to find what they need without hassle. Lean Supply Solutions states, “Without proper inventory management, finding products and managing shipping and receiving will be much more disorganized and challenging. It also increases the risk of damage to property since hazards are not clearly labelled and identified.”
Avoiding Automation
Many logistics operators don’t see the value in transitioning to a more viable, technologically advanced set of systems and don’t embrace the power of warehouse automation. From barcode data to conveyor belts and automated retrieval and picking solutions, automation is a great new step in the supply chain industry and can help revolutionise your business by boosting your productivity.